Introduction
You can use the Advanced Returns Management component in SAP ERP with SAP Extended Warehouse Management (SAP EWM) to manage returns items on storage bin level. The inspection of returns items is fully supported by the Quality Management (QM) component of SAP EWM. This integration improves the efficiency and transparency of the returns process.
In this blog I would like to compare 2 scenarios of ARM integration with EWM in comparing with Customer Returns process without ARM as listed below.
- Customer Returns Process without ARM
- ARM integration with EWM Process – Inspection occurs in ERP
- ARM integration with EWM Process – Inspection occurs in EWM
The testing version is S/4 HANA 2020 – EWM Decentralized.
Process Flow
Explain ERP Storage Location maps with EWM Warehouse Avail.Grp
Before we get into detail of each process, let’s have a look of current mapping between SAP ERP Storage Location and Warehouse Availability Grp & Stock Type as below.
We manage returns stock in ERP Sloc RETR firstly after receiving, upon inspection decision we will transfer stock to normal Sloc GRCV or Scrapping Sloc SCRP. And in EWM we have mapping Stock type for each Sloc. Try to keep the process simple so we only have 1 Stock type (F4/F9) per Avail.Grp for Returns & Scrapping.

Customer Returns Process without ARM
In this scenario, we assume that Inspection will be manage outside SAP and decision to change stock type after Inspection have to be done manually.
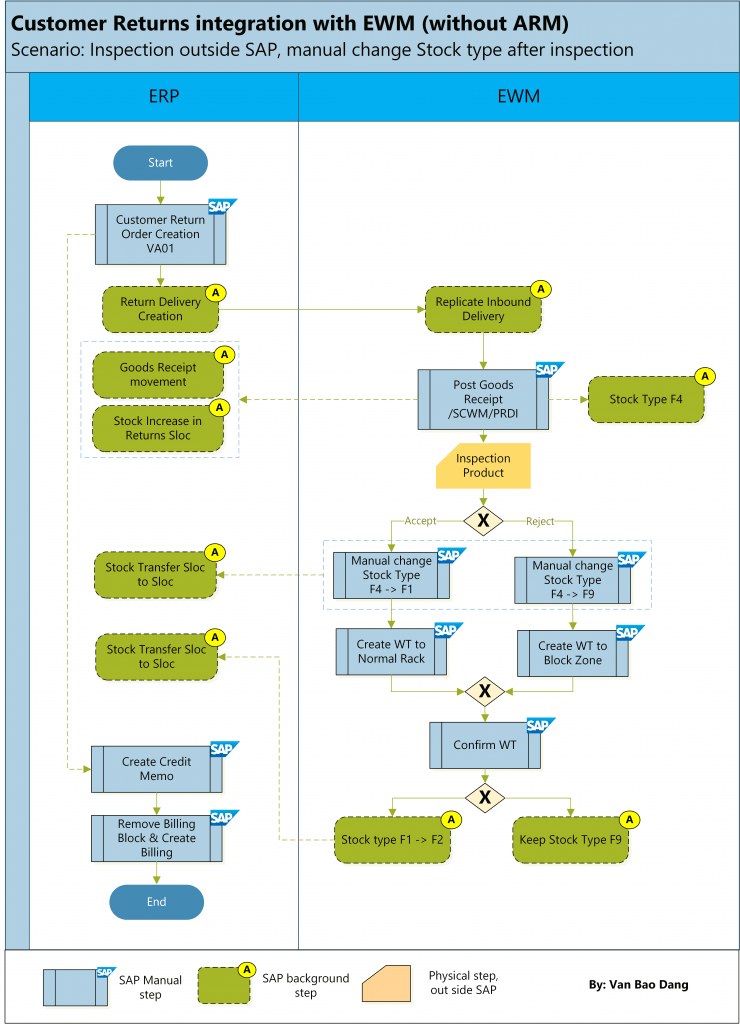
ARM integration with EWM – Inspection occurs in ERP
In this scenario, Inspection happens in ERP and inspection result is sent from ERP to EWM.
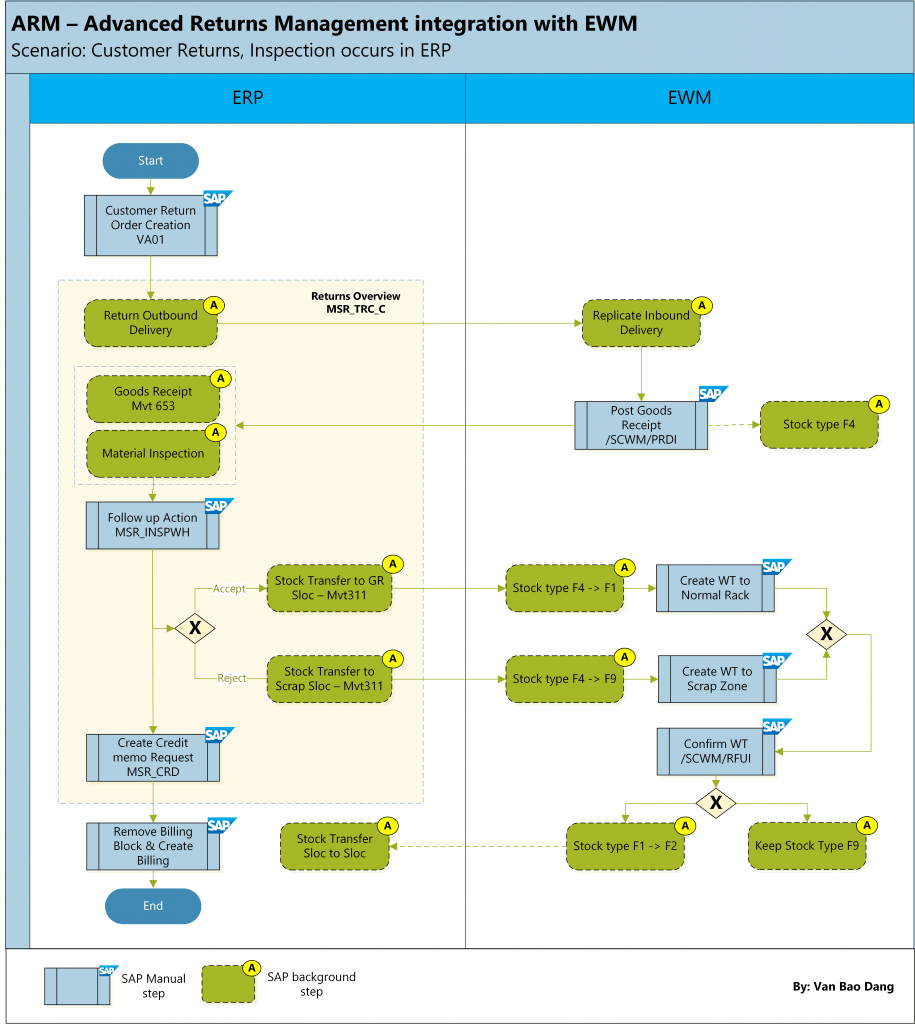
ARM integration with EWM – Inspection occurs in EWM
In this scenario, Inspection happens in EWM and inspection result is sent from EWM to ERP.
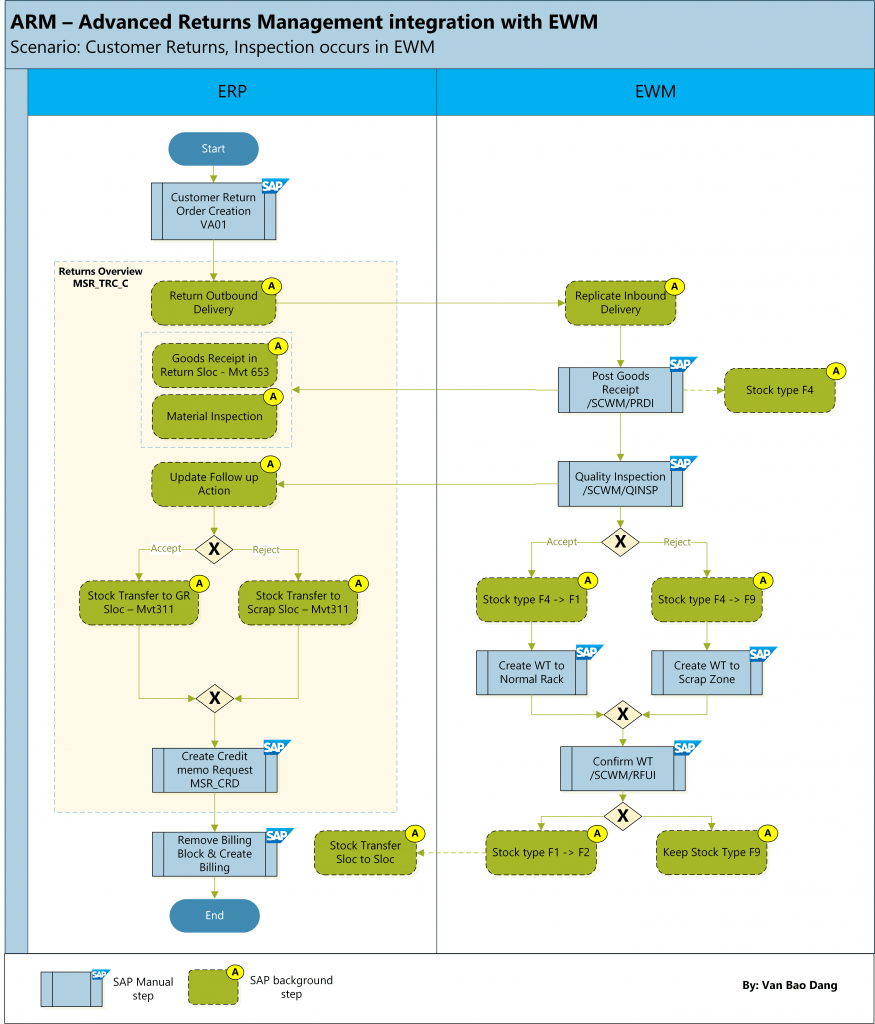
Testing
Because the limitation of my current EWM system setting, I can only describe the testing for scenario ARM – Inspection occurs in EWM with 2 Cases: Inspection Decision Accepted & Inspection Decision Rejected/Scrapping.
The testing for scenario ARM integration with EWM – Inspection occurs in ERP – You can reference to another blog that I attach the link in the Reference part.
Prerequisites
You have made the following settings in Customizing for Extended Warehouse Management:
- You have separated the posting of a decision and follow-up action and canceled an inspection under Cross-Process Settings -> Quality Management Basics -> Warehouse-Dependent Activation for Inspection Object Types.
- You have made the basic settings for inspection rule (master data) creation under Cross-Process Settings -> Quality Management -> Settings for Inspection Rules.
- You have defined a code group MSRDEC with assignment of allowed decision and follow-up codes (this has to be synchronized with SAP ERP) under Cross-Process Settings -> Result.
- You have set up QM for the sending and receiving locations under Cross-Process Settings -> Quality Management.
- You have maintain QM Inspection Rule under Q-Inspection Returns Tcode /SCWM/QRSETUP
ARM – Inspection occurs in EWM Process Flow Testing
Step 1: ERP Create Returns Sales Order
Tcode: VA01
Returns Sales Order is created with Follow-Up Action is “Receive into Plant” and Refund Control “Standard by credit memo request”.
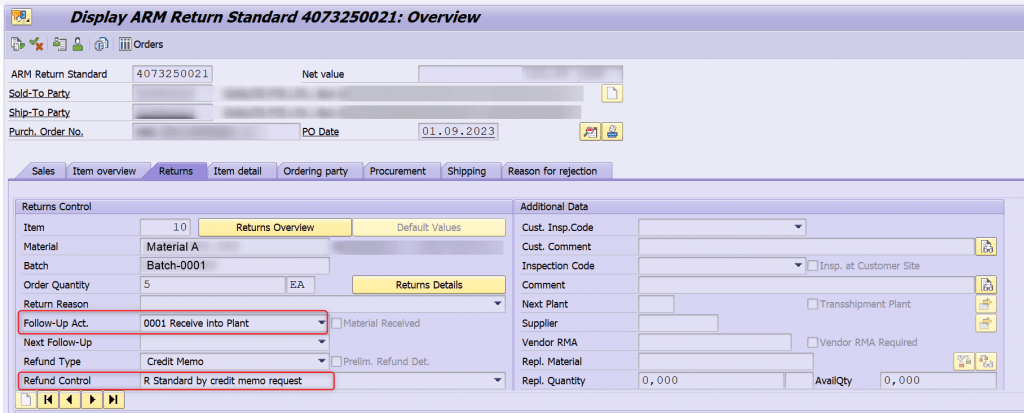
Step 2: ERP Outbound Delivery is created.
Tcode: VL10A
Outbound Delivery is created reference to Returns Sales Order, and receiving Sloc is RETR – Returns.
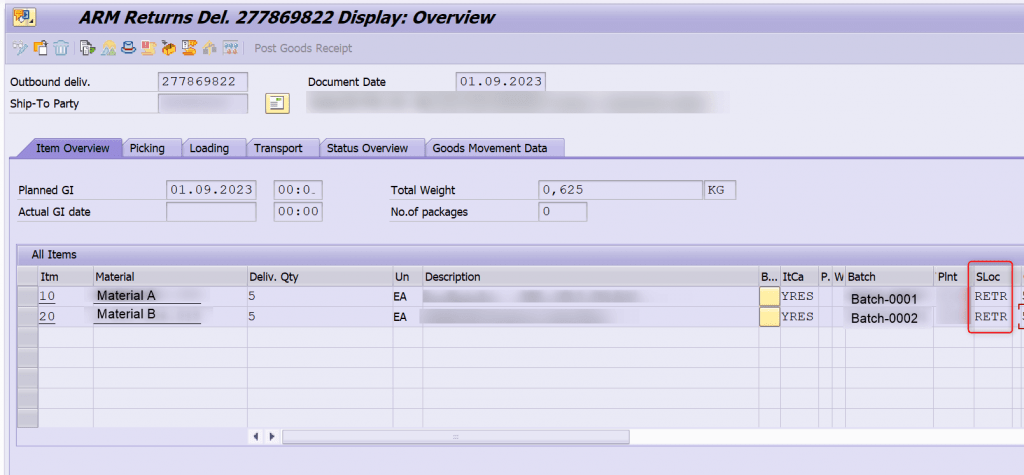
ERP – Check Customer Returns Overview – Tcode MSR_TRC_C
At this stage when Return Delivery is created, you can see Delivery number is updated in the Returns Steps and marked as Green – Completed, next step is GR marked blue as not yet process.
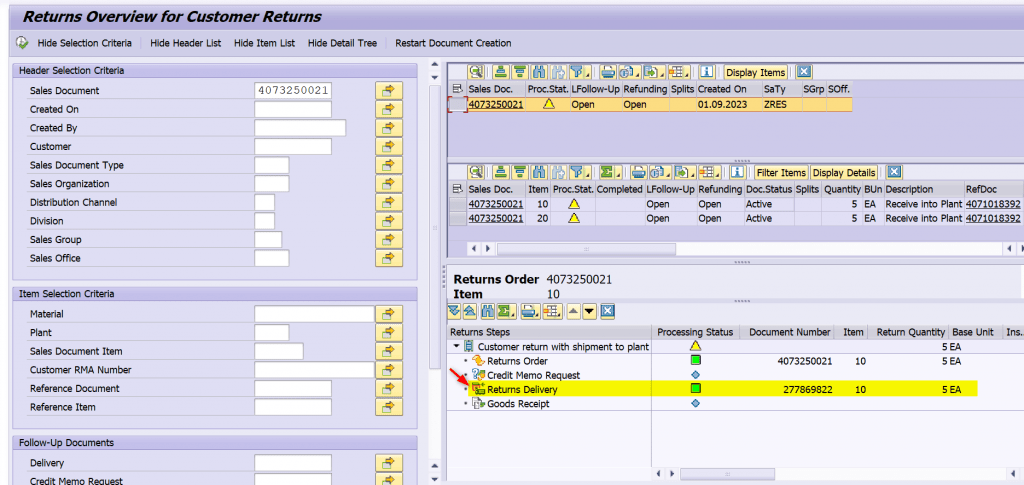
Step 3: EWM Inbound Delivery is replicated, Post GR
Tcode: /SCWM/PRDI
EWM Inbound Delivery is replicated and stock supposed to be posted in F4 – Returns stock type and keep in QI-ZONE.
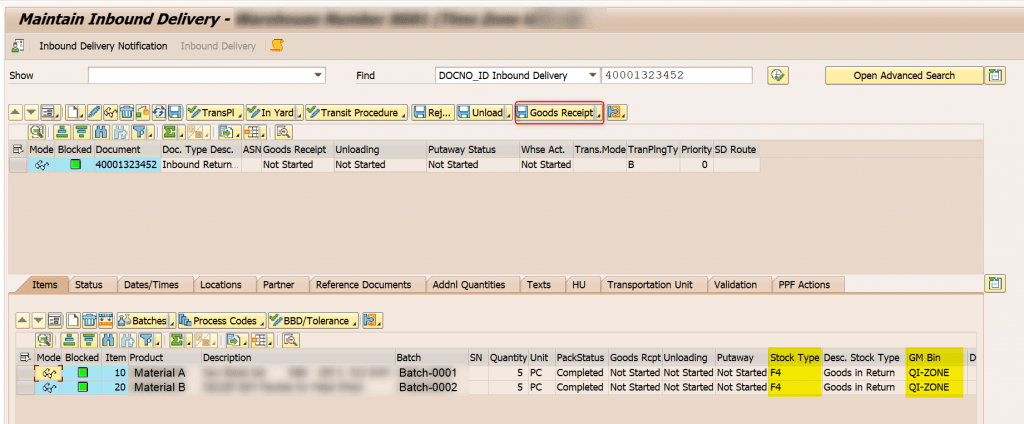
Post GR and GR status is completed.
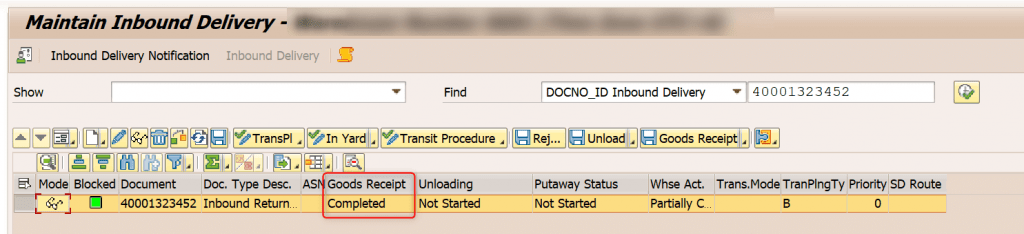
ERP – Check Returns Overview
After GR posted in EWM, it sends update to ERP and Goods receipt movement is created and marked as Green – Completed, next step is Inspection.
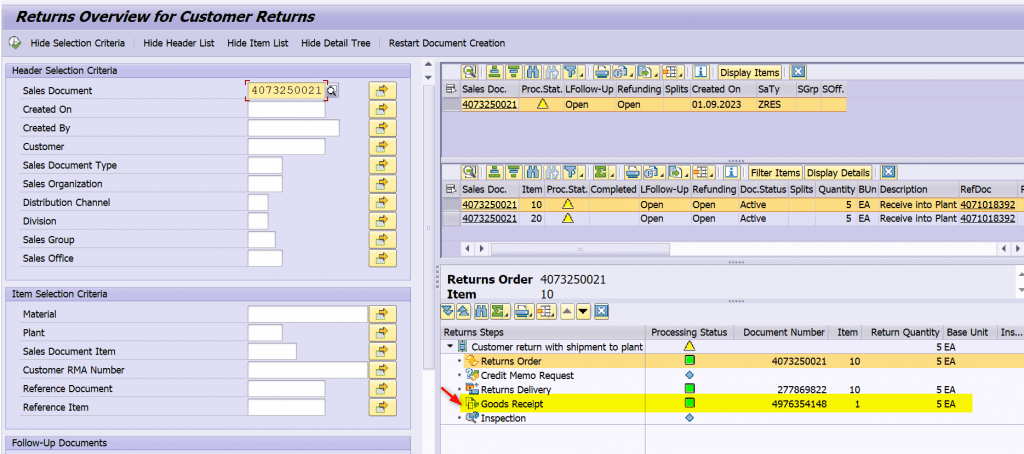
Display GR Document, it’s posted with Mvt653 and to Sloc RETR.
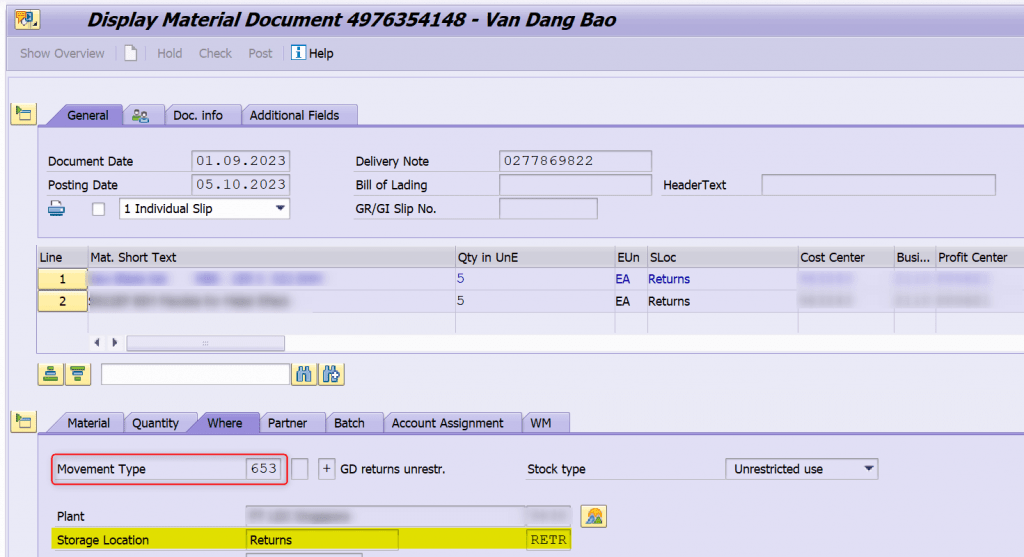
Step 4: EWM Inspection
Tcode: /SCWM/QINSP
There are 2 Items in Delivery, I will set Item 10 – Material A as Inspection pass and Item 20 – Material B as Inspection fail, then we can compare the difference.
Item 10 – Perform Inspection Decision: Accept – Quality check passed.
First step to create new HU because current HU is the dummy one. Then choose the Decision as 0001 – OK, Accepted; and assign Dest. HU as new created HU.
Note the Inspection Type before making Decision is A.
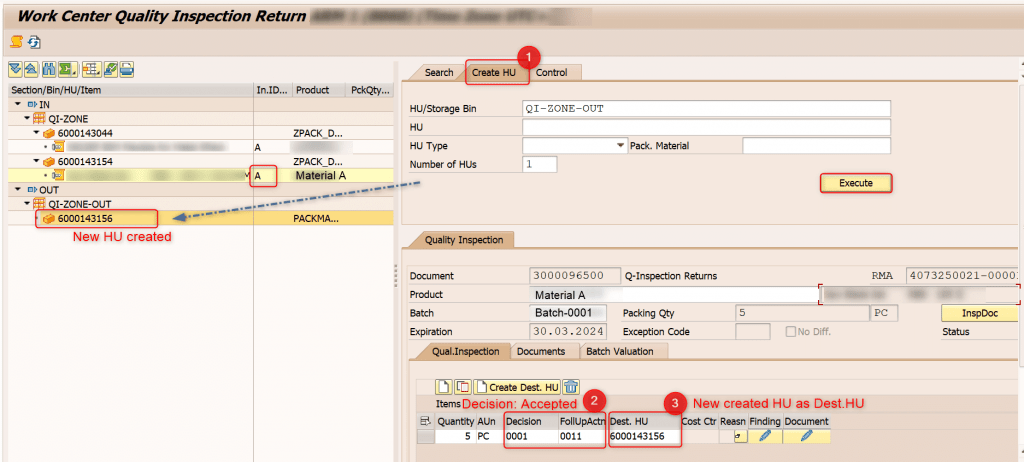
Save the inspection decision and you can see Inspection Type changed to C now. You can mark Completed Process Step for HU if storage processes related.
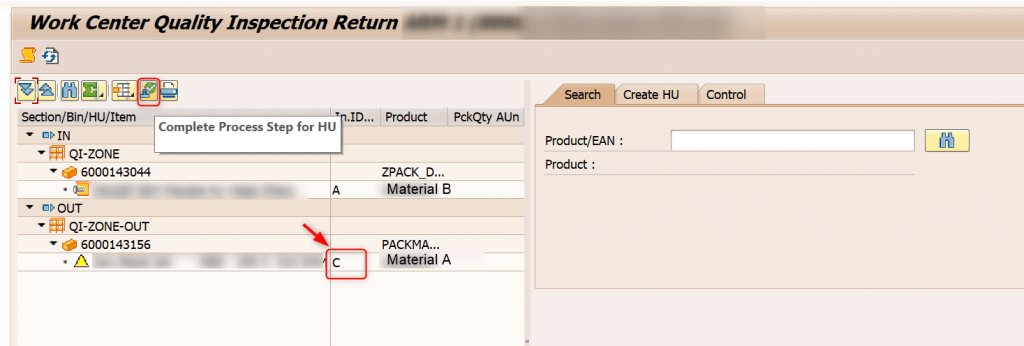
EWM – Stock Overview: Material A is updated as F1 – Goods in Putaway.
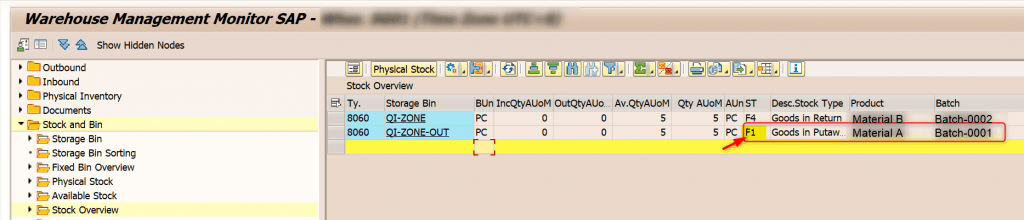
ERP – Check Returns Overview
Inspection result is sent from EWM to ERP and updated in Returns Steps. Here Inspection result and Transfer Posting are marked Green – Completed. Next step in ERP is to create Credit Memo.
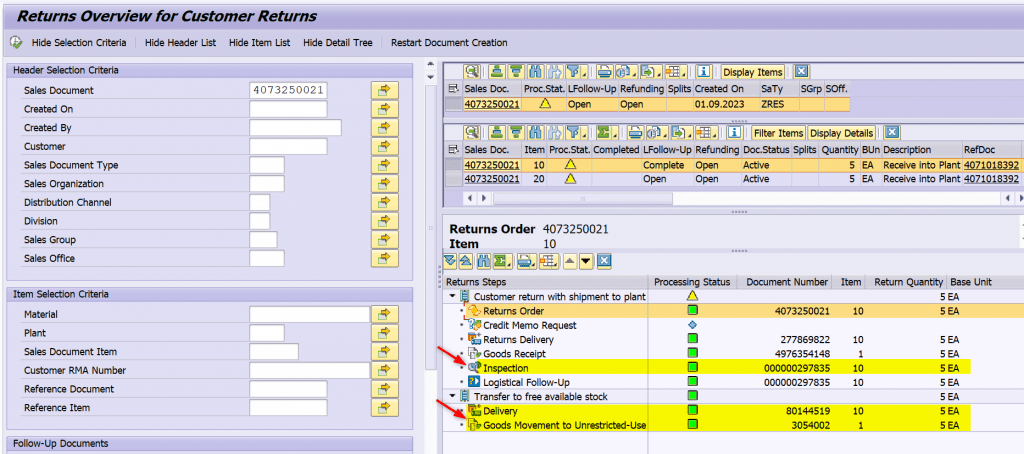
Display ERP Inspection, Follow up Activity is “Transfer to Free Available Stock”.
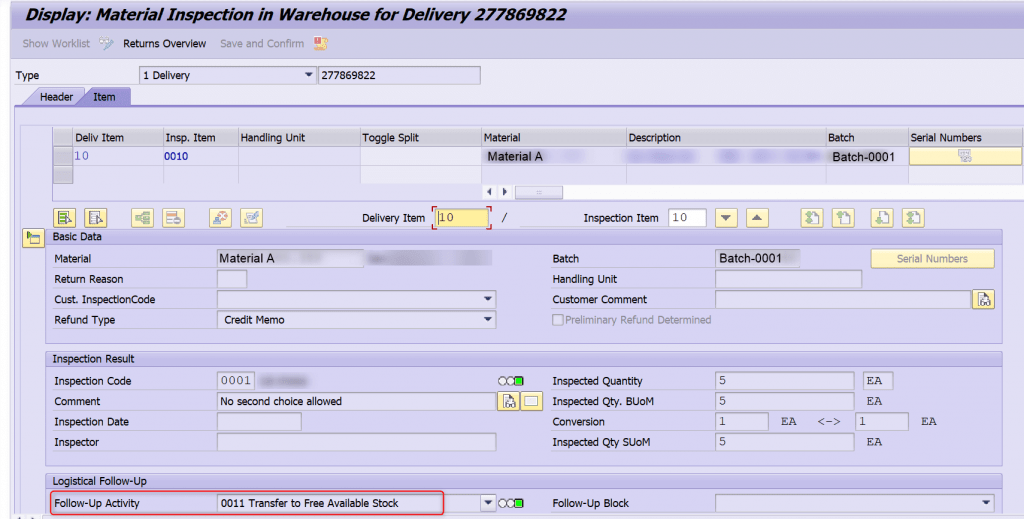
Display Transfer Posting, it transfers from Sloc RETR to GRCV.
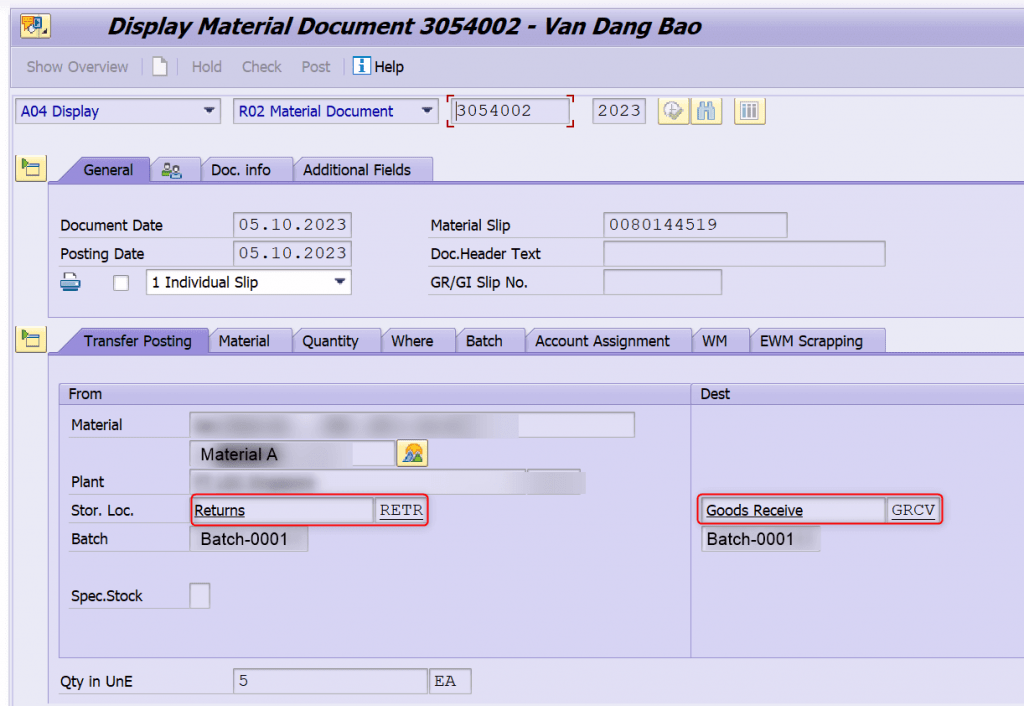
Item 20 – Perform Inspection Decision: Reject/ Scrapping – Quality check failed.
First step to create new HU, then choose the Decision as 0003 – Scrapping and assign Dest. HU as new created HU. Note that Inspection Type change from A to C after Save Inspection result.
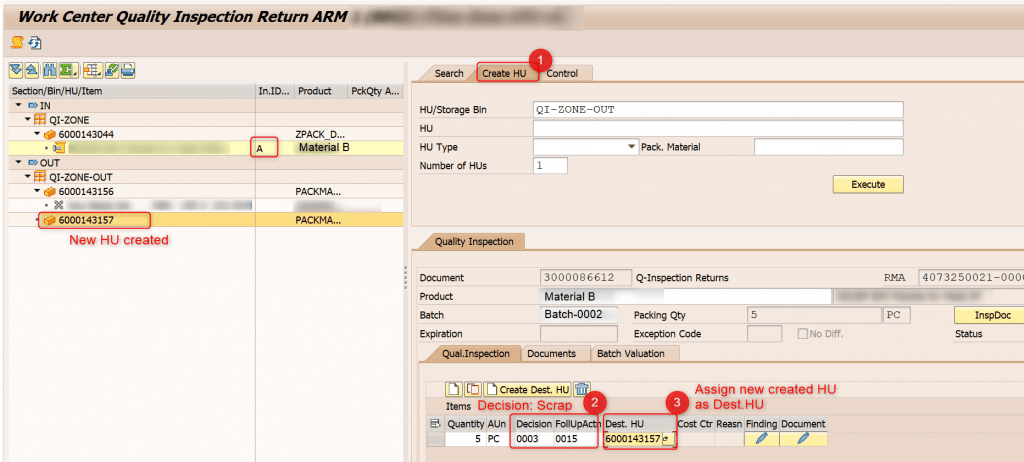
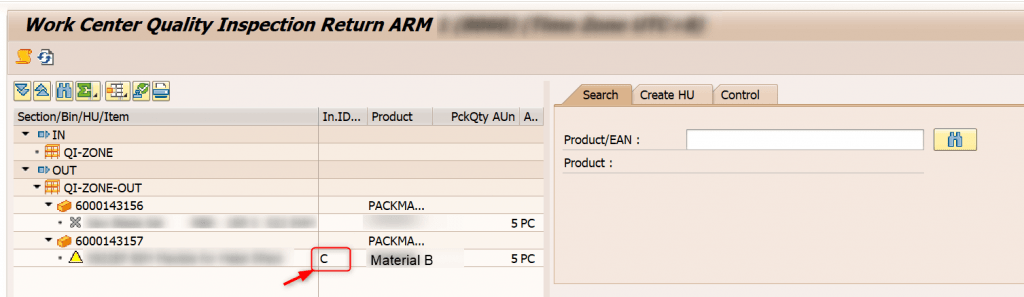
EWM Stock Overview, stock type is changed F4 -> F9.
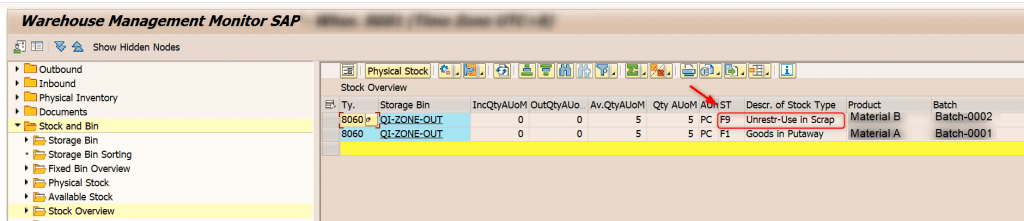
ERP – Check Returns Overview
Inspection result is sent from EWM to ERP and updated in Returns Steps. Here Inspection result and Transfer Posting are marked Green – Completed.
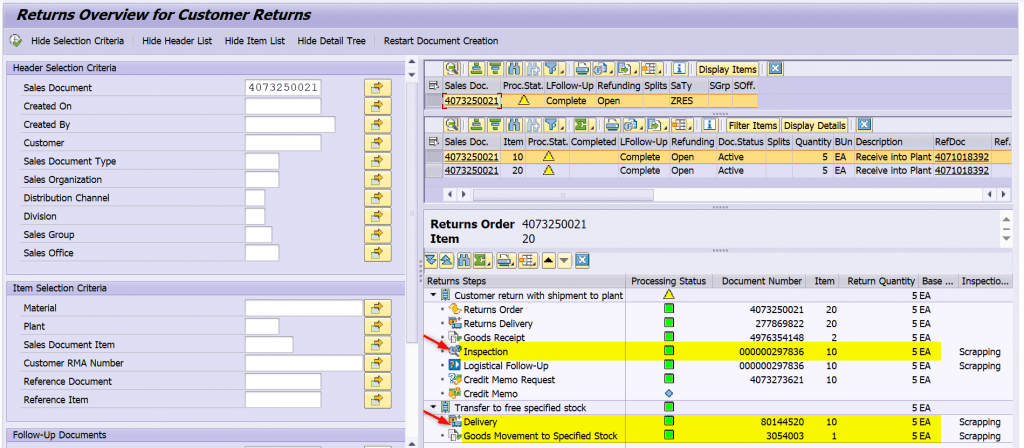
Display ERP Inspection, Follow up Activity is “Transfer to Specified Stock”.
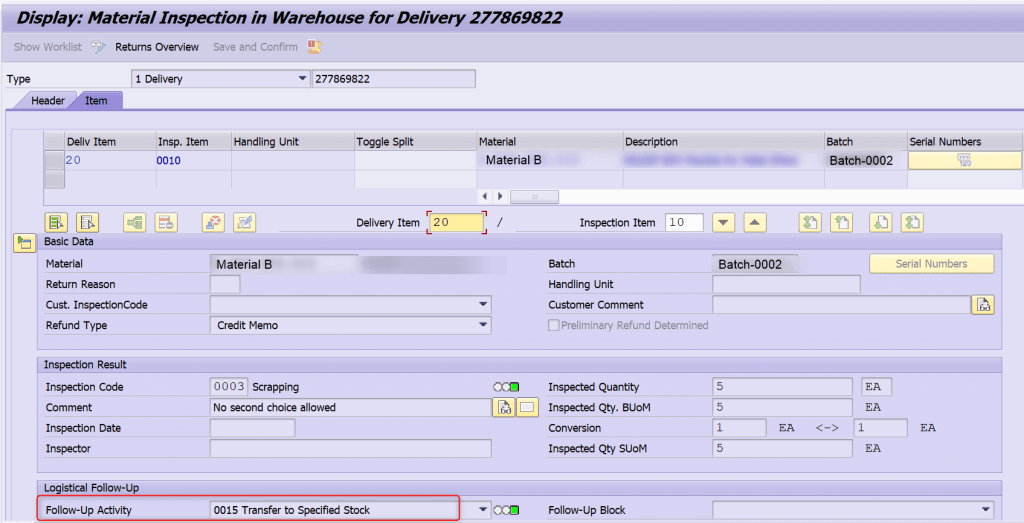
Display Transfer Posting, it transfers from Sloc RETR to SCRP.
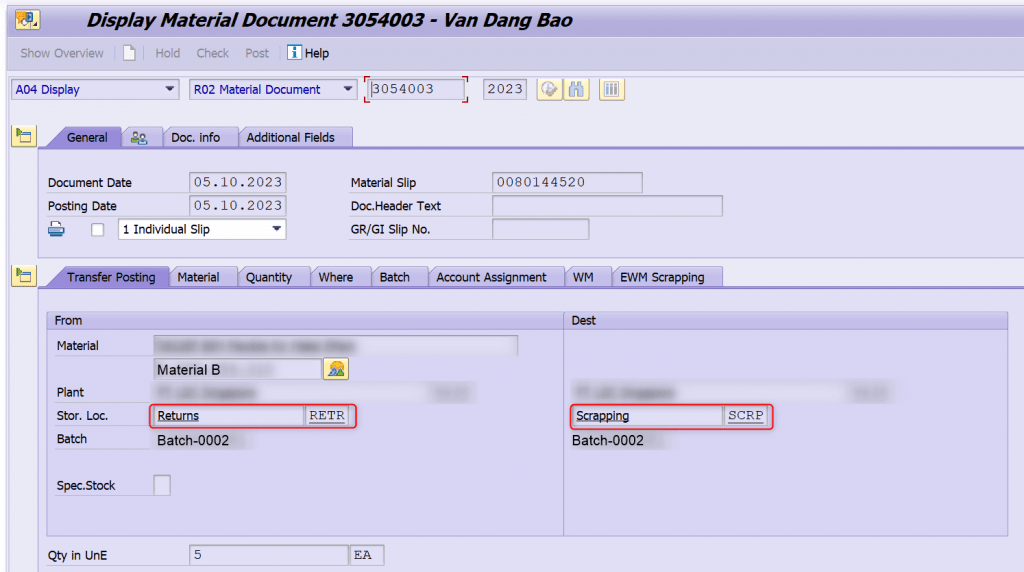
Step 5: EWM Create Warehouse Task for Putaway & Confirm WT
This step is managed in EWM to finish EWM putaway step and has no impact to further Credit Memo step in Returns process in ERP, means Credit Memo step can happen in parallel.
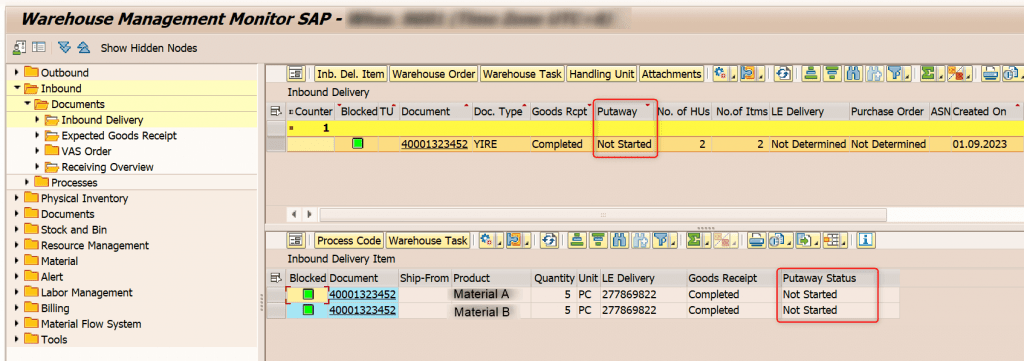
Create WT as Follow-On Function in Inbound Delivery and confirm WT as normal.
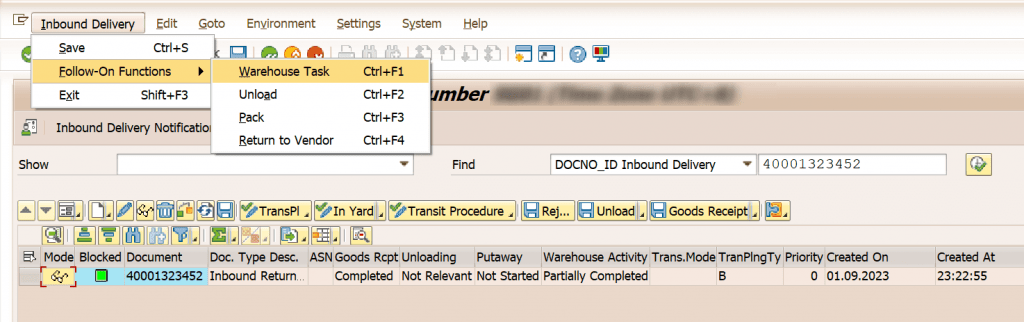
EWM – Stock Overview: After Putaway Material A to Normal Rack, Stock type change F1 -> F2; Putaway Material B to Clearing Zone for scrapping, Stock type has no chance.
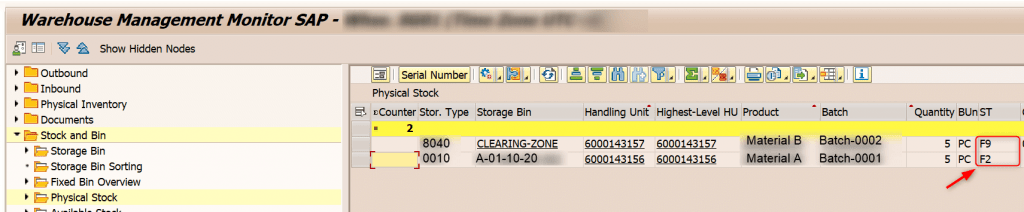
Step 6: ERP Process Credit Memo & Payment
Those steps belong to Accounting department which I don’t get in detail. Statuses are updated in Returns Overview as well.
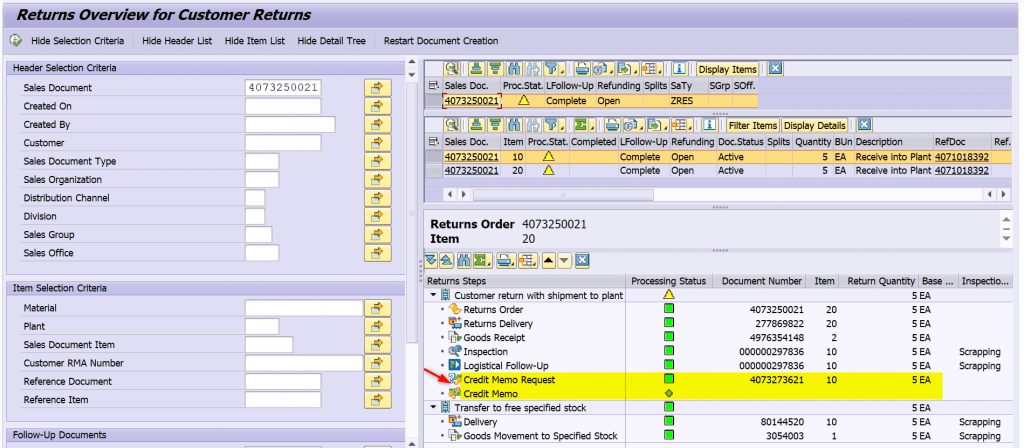