Product availability check helps to fulfill the customer delivery/promise date. The system automatically runs the product availability in background ( for example at sales order, delivery level) taking into consideration the requested delivery date and determines when the product will be available. Based on the material availability date, picking/packing, transportation time a delivery date on which quantity of goods can be delivered is proposed. After the check is executed, the quantity is reserved and unavailable for any other requirements.
Availability Check at Sales Order
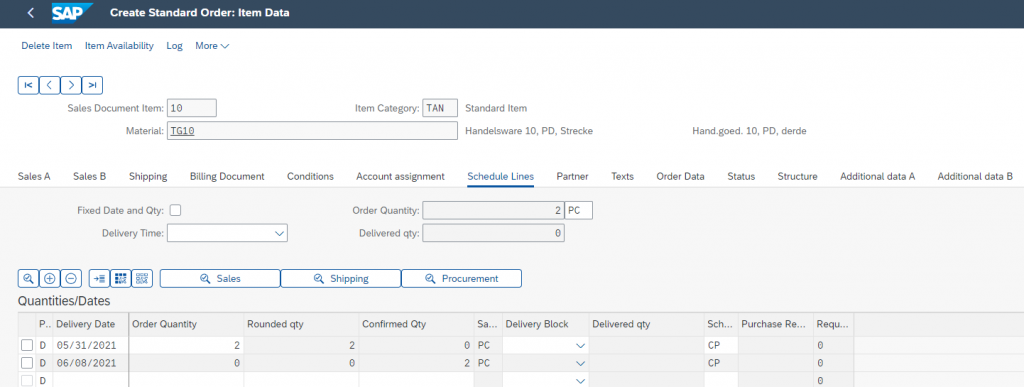
Select the confirmed item and go to shipping.
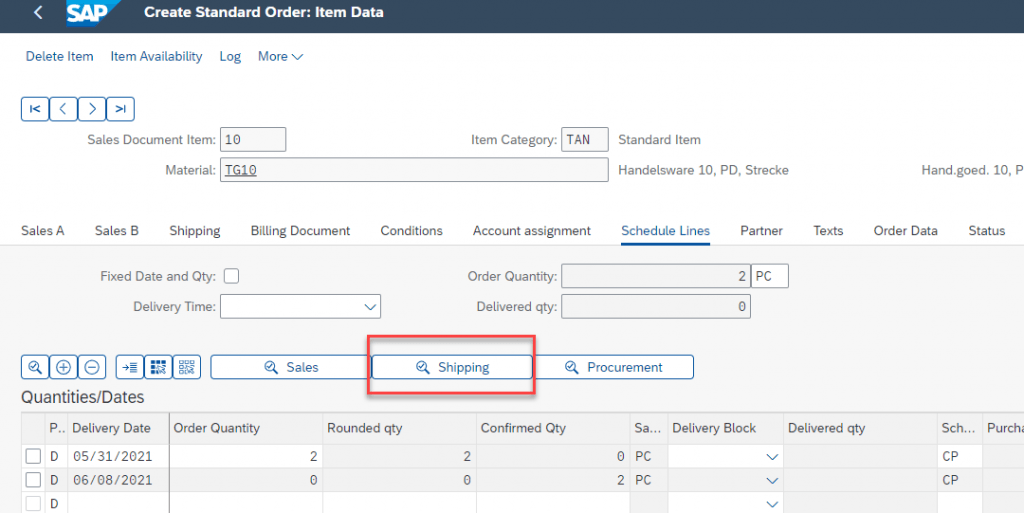
Here we can see how requested delivery date has been calculated (Using Forward/Backward Scheduling). Based on the material availability, transit time, loading time and pick/pack time the delivery date has been calculated as 8th of June 2021 (06/08/2021)
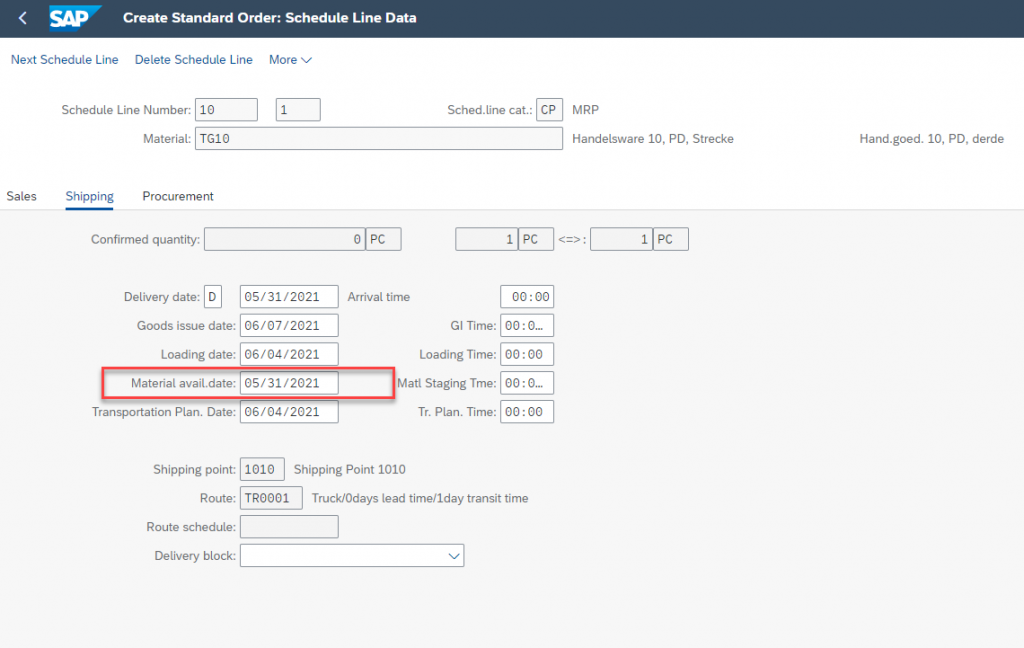
In the sales order we can also check Display availability to see how system confirms the stock for the new requirement (sales order in this case).

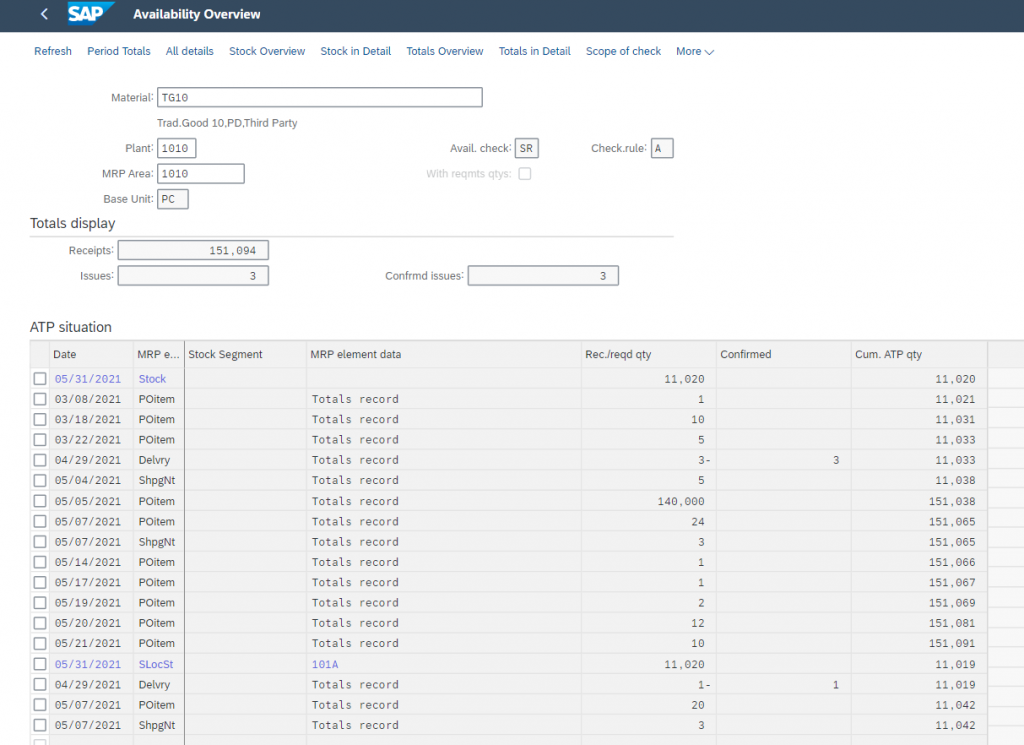
The date in Availability for MRP element Customer order will be the material availability date.
Monitor Product Availability App
Availability overview can also be reached by Monitor Product Availability app. This is a stand-alone app to check the availability for an Item
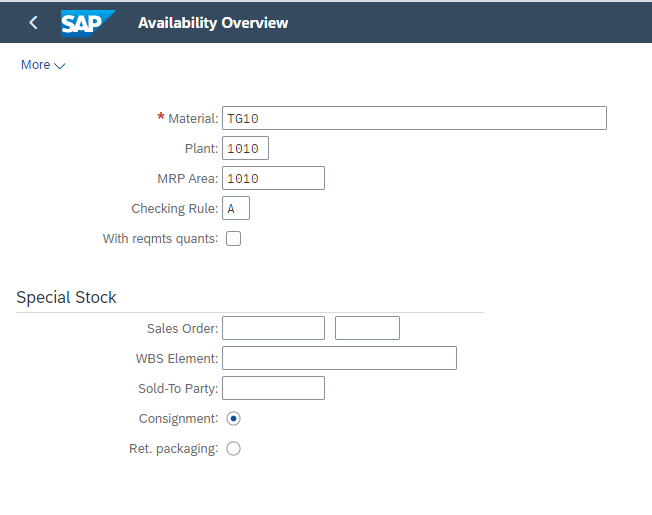
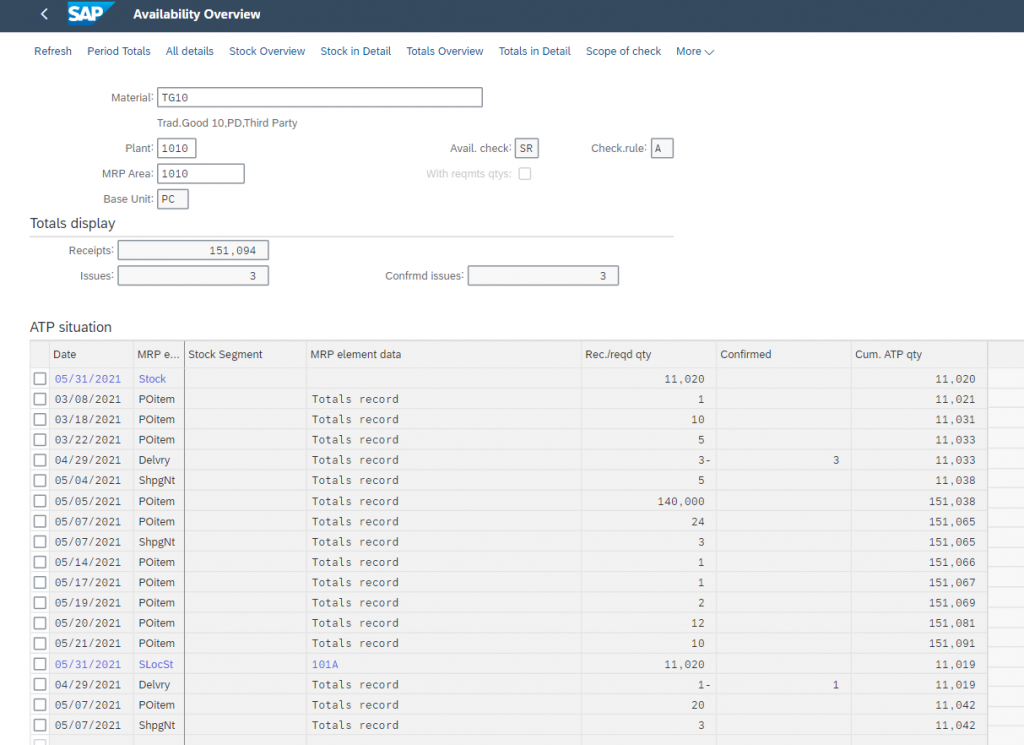
Scope of Check
In the app we see “Scope of Check” if we click on this we can further see which stocks, issues & receipts are considered while confirming the stock.
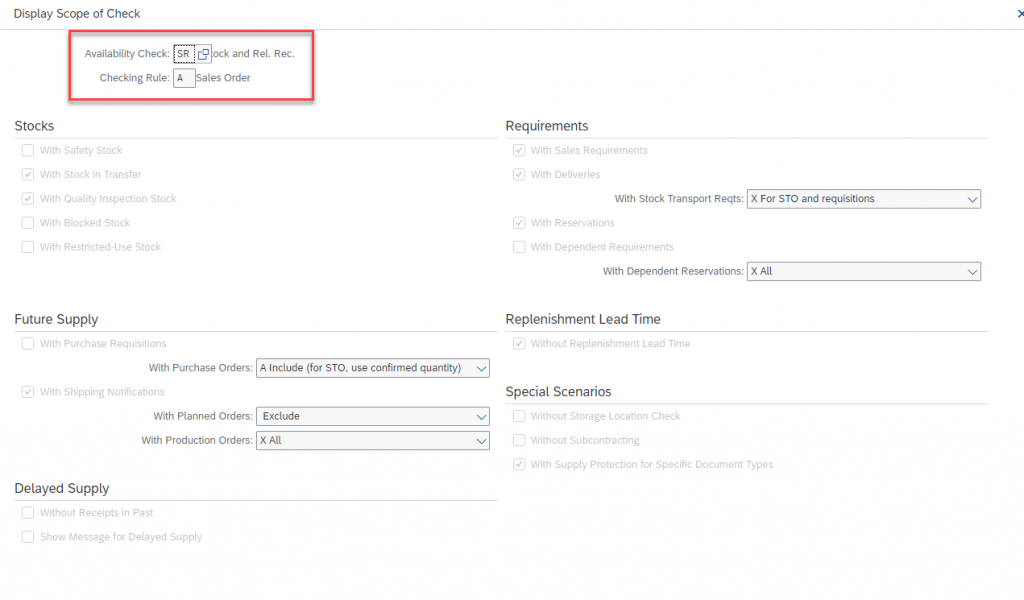
In the scope of check, we can define which MRP elements such as requirements, stocks, future supply, replenishment lead time etc. to be considered. For example, if safety stock is checked then system can confirm based on this else safety stock will not be considered for availability.
F1 will give details on each element.
Scope of check is the combination of Availability check and Checking Rule.
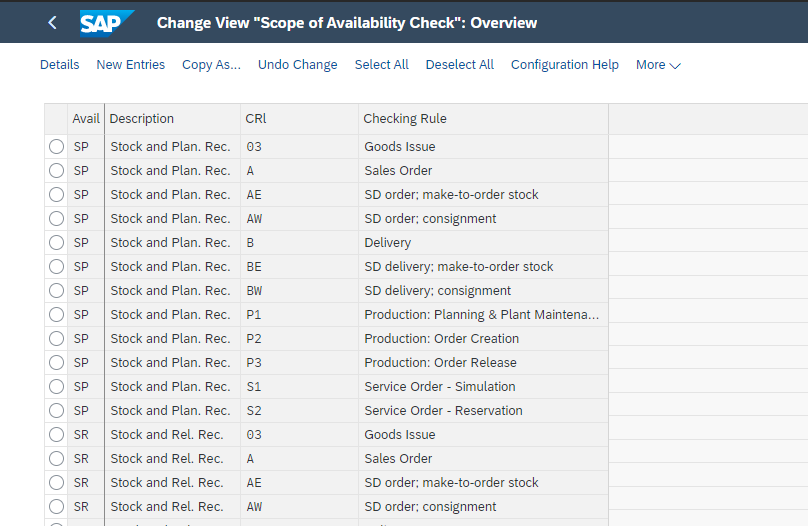
In the material master, Availability Check field is to specify the receipts and requirements to be considered when checking sales orders and deliveries.
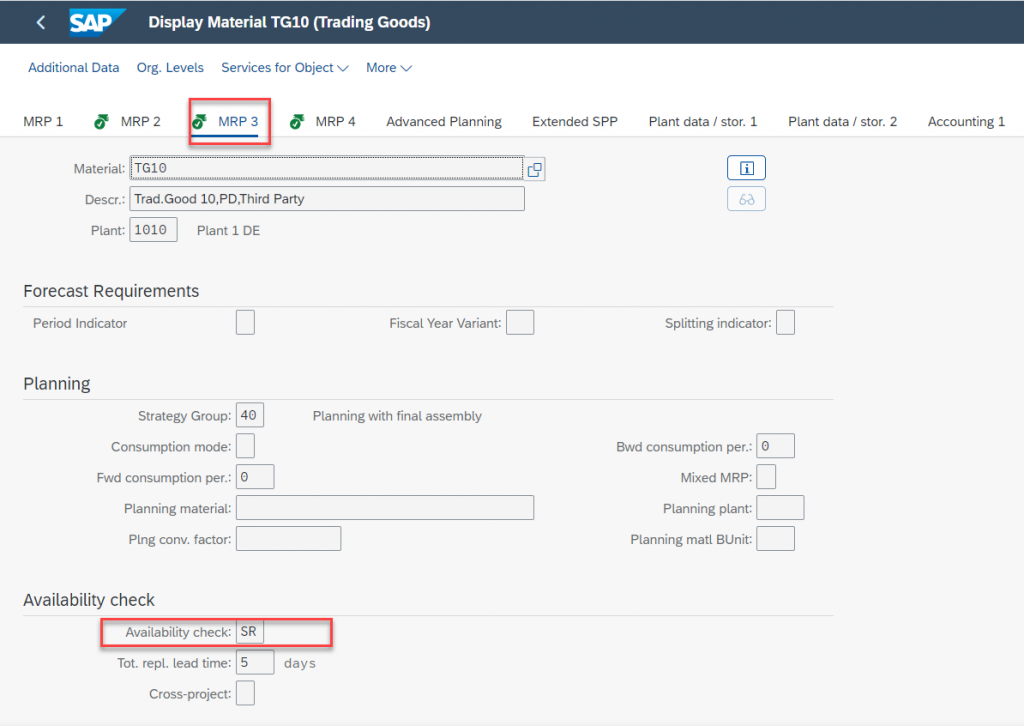
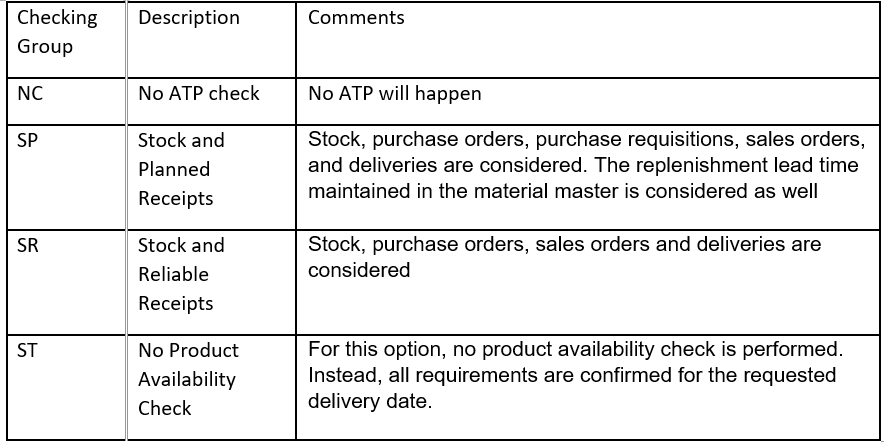
Checking rule is transaction based, i.e. In sales, if we are creating the sales order, then it is A, if delivery then it is B.
When we run transaction like create sales order or delivery system automatically chooses checking rule. But in Monitor Product Availability since this an independent app we specify the checking rule.
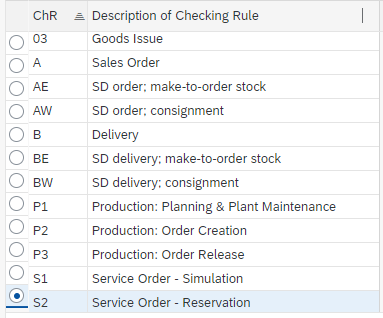
Availability Overview
- In the section ‘Totals display’ we can see the total amounts of your ‘Receipts’ (stock is included), ‘Issues’ and ‘Confirmed issues’.
- The lines in blue correspond to the different levels on which the ATP check is carried out. We have four levels (plant, storage location, batch, batch/storage location). When the levels are maintained in the document then we will see the document on different levels and the ATP check is carried out on those levels
These two deliveries are at Plant level since no storage location is entered in delivery.
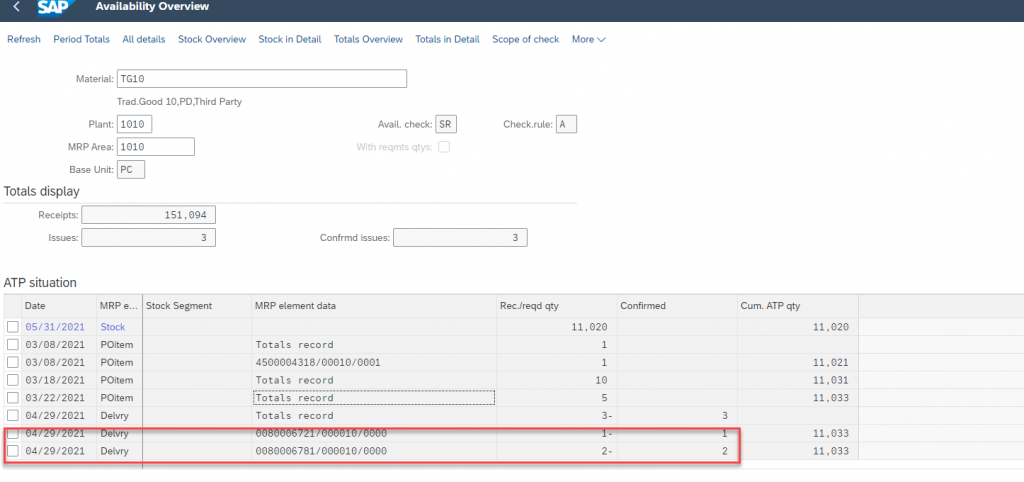
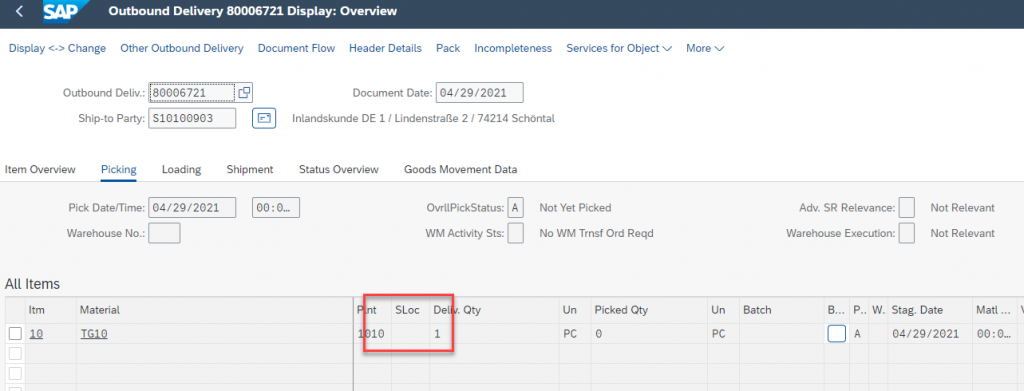
Now we maintain the storage location and see the same delivery at storage location level as well.
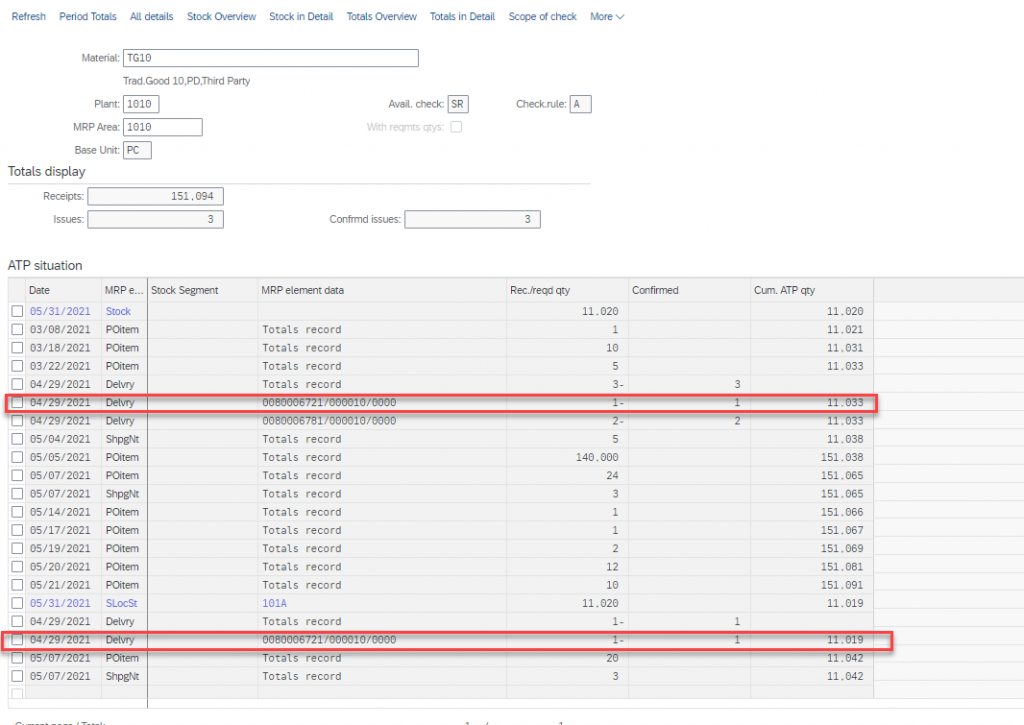
- The cum. ATP qty will always show the maximum qty that could be confirmed on this date if a simulated requirement was entered on this line.
As the below example on 31.05.2021 we have cum ATP quantity as 11,020 to confirm ( Please make note this stock can be different from actual stock as we can see in stock overview or stock requirement list. It is because Availability takes into consideration various MRP elements and then show the stock that can be committed to the customer )
Similarly, on 8th of March since we have incoming stock from PO we have cum ATP quantity as 11,021 to confirm
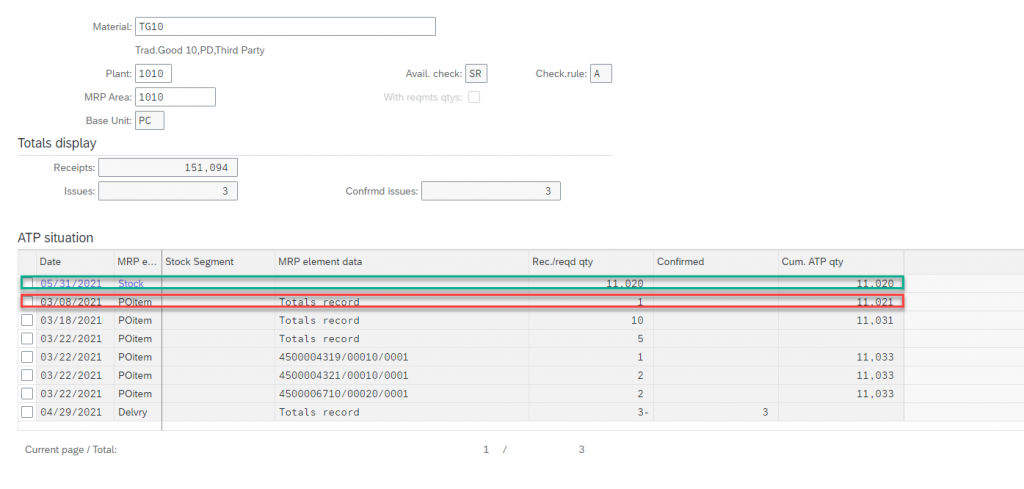
- The cum. ATP qty will be increased on the date of a receipt if the receipt is greater than the issues below it(until the next receipt).
Here in this example we see on 22.03.2021 MRP element PO has 3 as incoming quantity and MRP element Delivery 29.04.2021 has outgoing quantity as 3 but still the cumulative quantity has not been increased from 11031 to 11033(3 PO items) and then reduced to again 11031 ( 3 delivery)
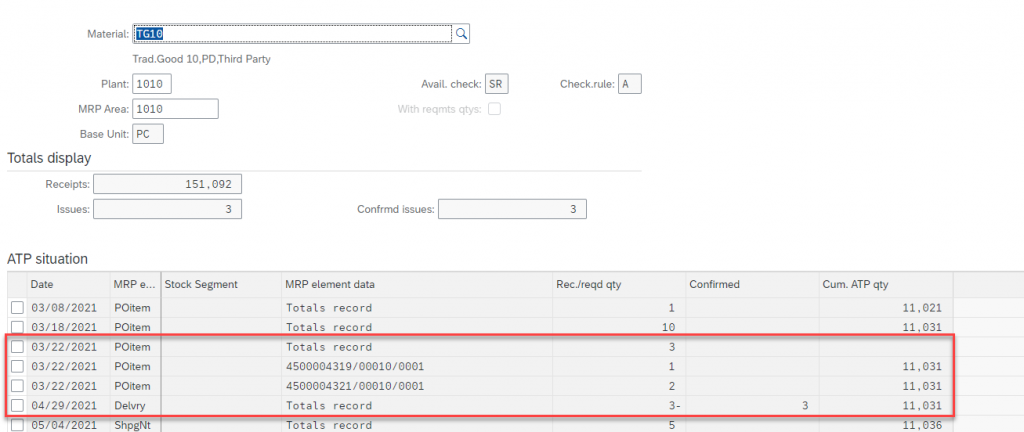
Now we create a new PO with delivery date as 20.03.2021
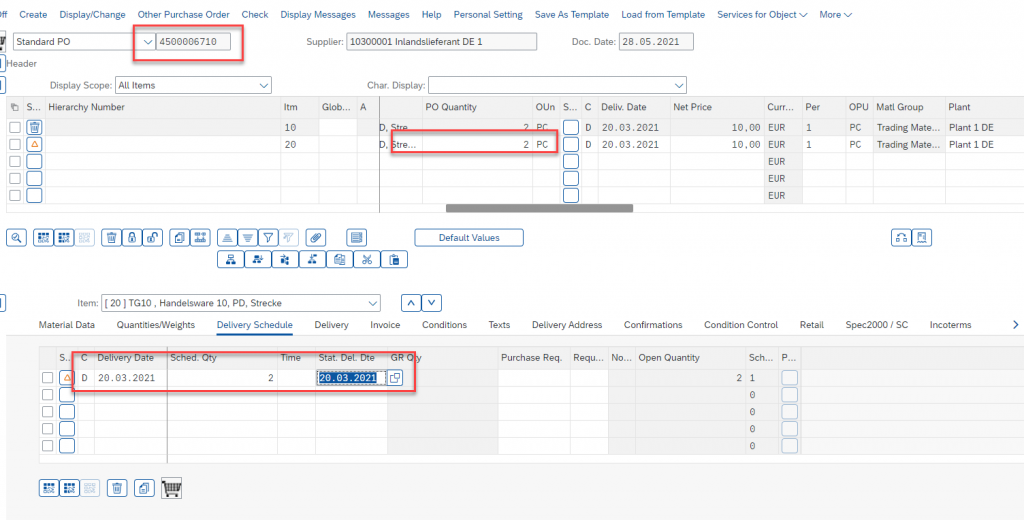
Since as per factory calendar 22.03.2021 is holiday we have the date in ATP as 22.03.2021and the quantity now has increased to 11,033
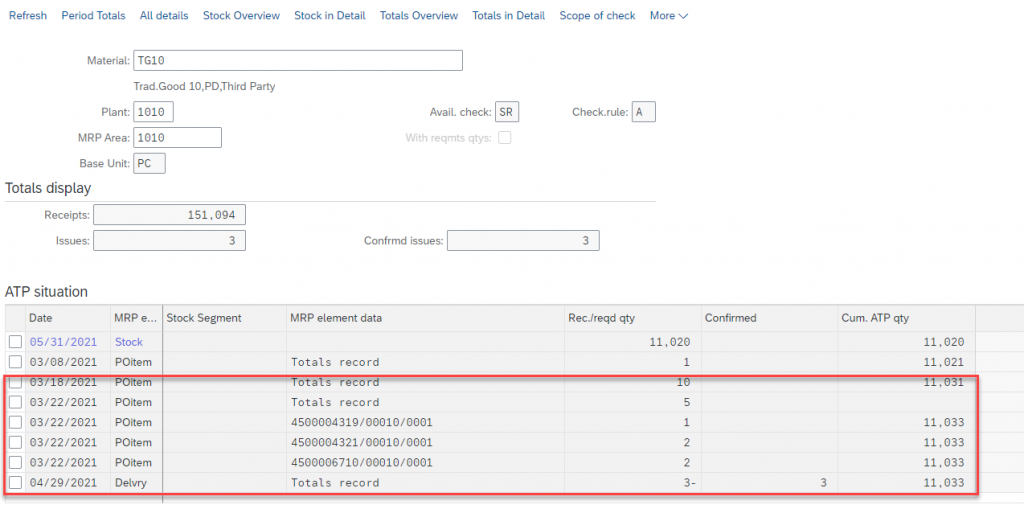
- The cumulative ATP qty cannot be greater than the figure for Total receipts – Total Confirmed Issues. Otherwise we can get any over confirmation.
- Details of MRP Element.
The first screen is totals Overview. To view details of the MRP elements. We can click on All details, once we click, we can see details of all the documents like PO’s, Deliveries etc. for all MRP elements. Or
To see a particular MRP element, we can click on it.
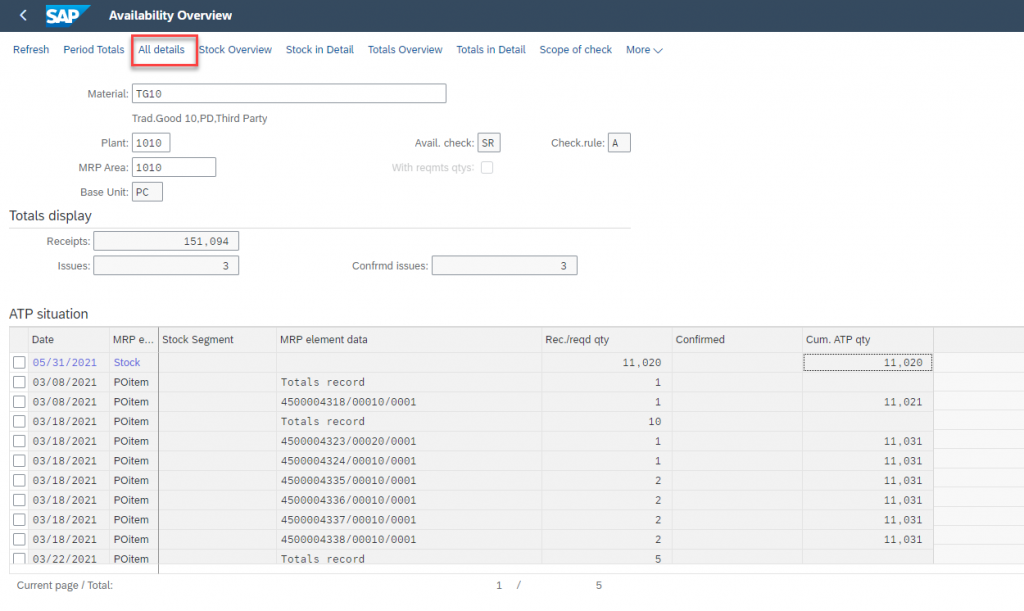
Also, we can navigate to documents directly from the Availability Overview.
Select the element and right click and Display MRP element.
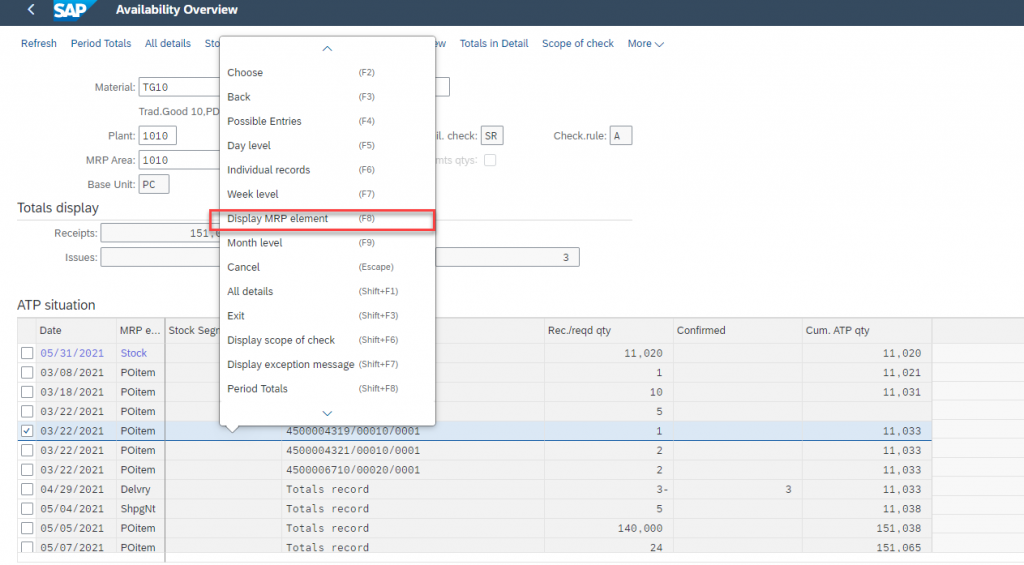
For MRP elements do F1 on MRP elements to get full definition
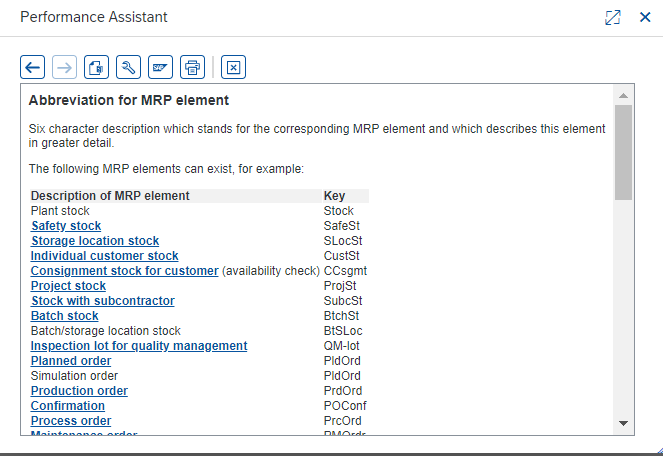
- Click on Period Totals and see availability Monthly, Weekly or Daily
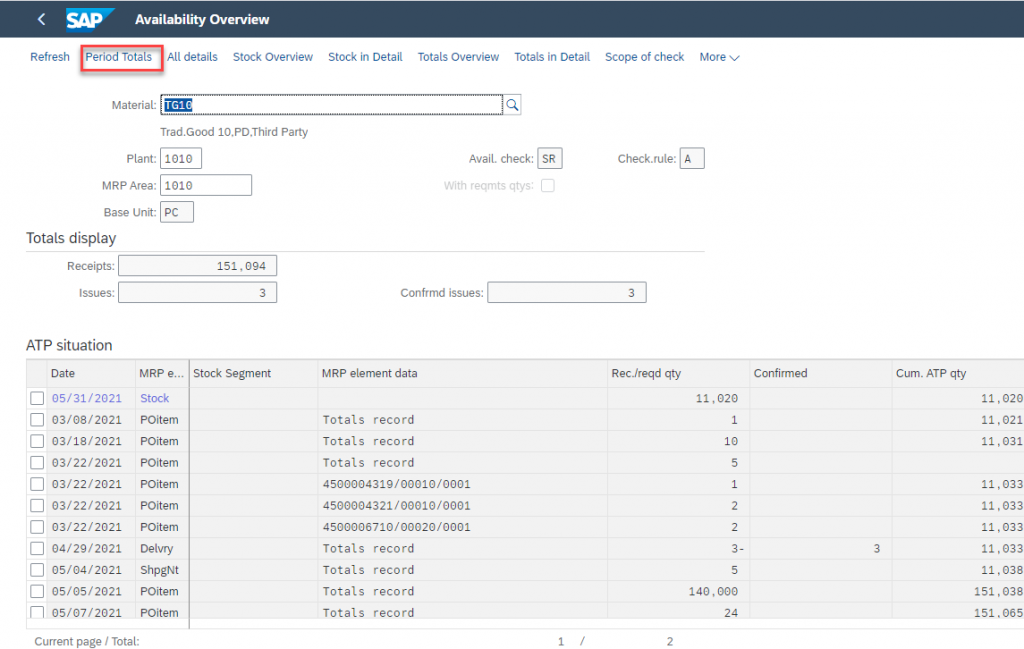
