Trigger Point: SAP trigger point is an object, which is assigned to an operation in routing in order to trigger a certain function. We can trigger certain business functionality using SAP trigger points when an operation or a production order statuses are being changed.
For example, we can trigger workflow to production manager when scrap is recorded in the production or we can create another order or operation when rework is recorded, etc. We can trigger production order relevant functions based on production order status (system or user) only.
Requirement: We have a list of operations for our finish product namely as CED coating, Assembly, Painting & Packing. The Painting operation is an automated process done with robot painting. If there is any painting rework then a labour do the manual painting on rework part & then Packing operation is processed. This is the regular process followed & there is rework in every manufactured lot.
Pre-requisites:
1. Create a Control Key with rework indicator active.
Control key: It is an user-defined key that determines how any operation will be handled at time of order processing and in product costing. There are different function which can be activated e.g. Scheduling, Print, Cost, Rework, etc.
As per the requirement, check the rework indicators. For system to consider any operation as rework operation, Control key with rework indicator checked should be used.
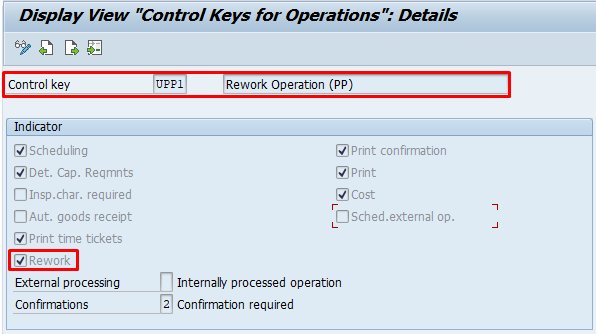
Note:
- Initially, A rework operation is not taken into account when scheduling task lists.
- If rework operation is last operation, then no automatic goods receipt can take place for the rework quantity. You must manually post the goods receipt for the quantity successfully reworked.
2. Create a ROS for rework (T-code-CA11).
First, create a paint rework work center for labour to record activity data.
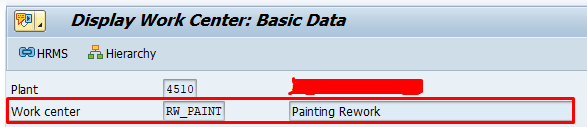
Assign this rework work center to rework operation of reference operation set (ROS). This ROS will be used for reworking paint defect manually.
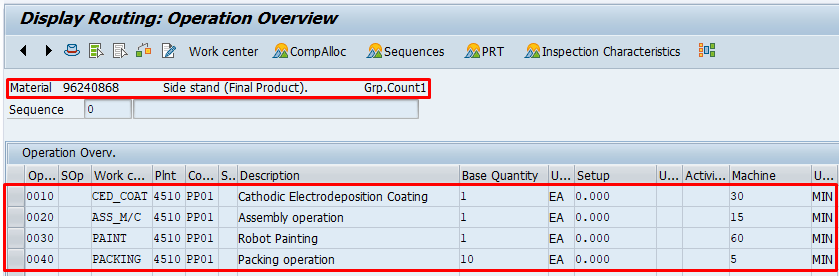
3. Create Trigger Point (T-code-CO31)
In trigger point select, function as Insert reference operation set. After selection insert ROS function assign the ROS group in parameter tab. Also, you can give after which operation you want this ROS to be inserted. In our case operation 0030 is painting operation & rework will be performed after painting operation. Hence, we will assign after operation as 0030.

Routing Setup:
Go to operation overview screen>>>click on go to>>>select trigger point overview.
Assign the trigger point to painting operation.
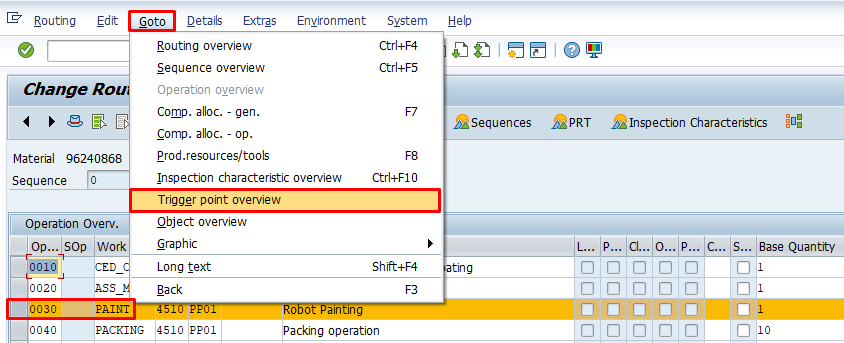
Click on StdTrgPoint to assign already created trigger point.
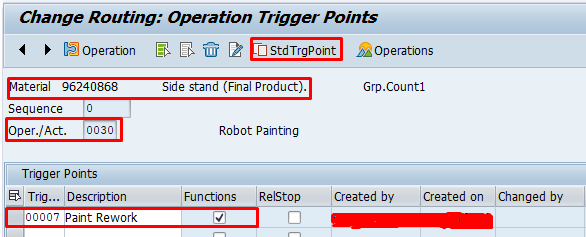
Test scenario:
Assume, We have a production order of 1000 qty. for 96240868 Side stand (Final Product) & in that we have found 50 qty. that need to be reworked for painting.
First, do the following steps:
- Create a production order with standard order type for production (PP01).
- Release order.
- Good issue to order.
- Confirm the first four (OP10, OP20) operations.
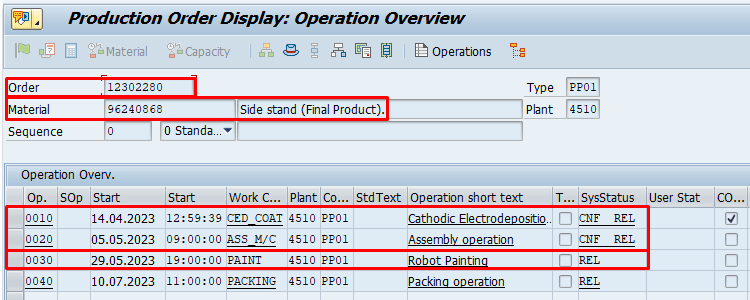
- Go to confirmation of painting operation (CO11N).
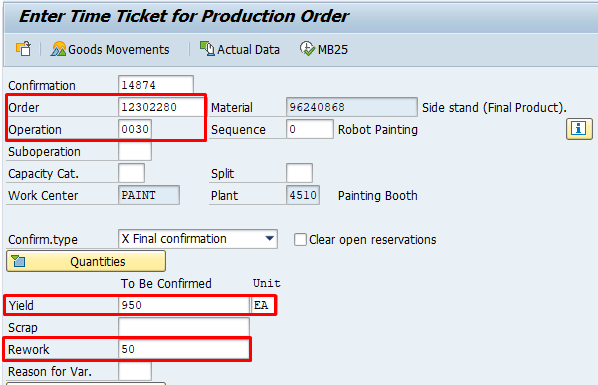
We had a production lot of 1000 qty. In first two operation (CED coating & Assembly) there was no rework rejection. In third operation (Painting) confirmed ok quantity was 950 qty. & there was rework of 50 qty. Once we save the confirmation with Rework quantity. Trigger point will be triggered & rework operation of reference operation set (ROS) will be assigned to production order. In that rework operation, operation quantity will be 50 qty. (rework quantity of paint operation).
As we are using manual trigger point, That’s why system is giving this pop-up. Whether you want to execute the trigger point for rework operation or not.
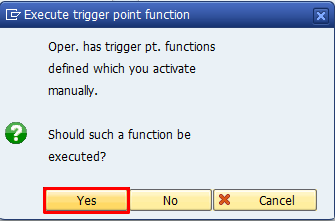
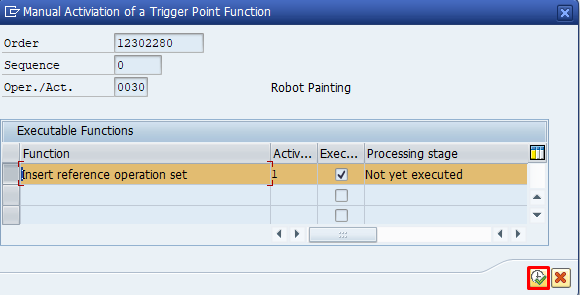
Select the function & click on execute.
After executing, confirmation will be saved & rework operation will be added to production order.
- Display Production order:
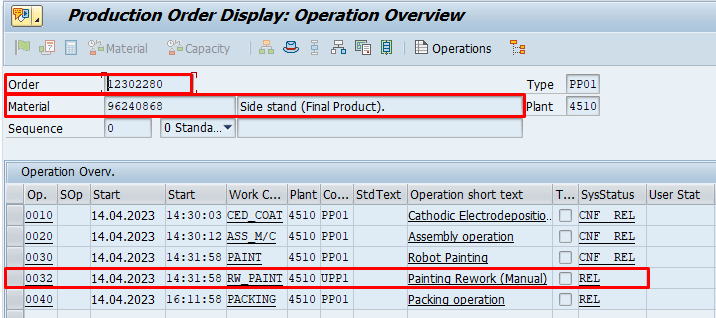
We can observe that after OP30 an operation has been added as painting rework manual OP32.
- Confirm the rework operation after completion.
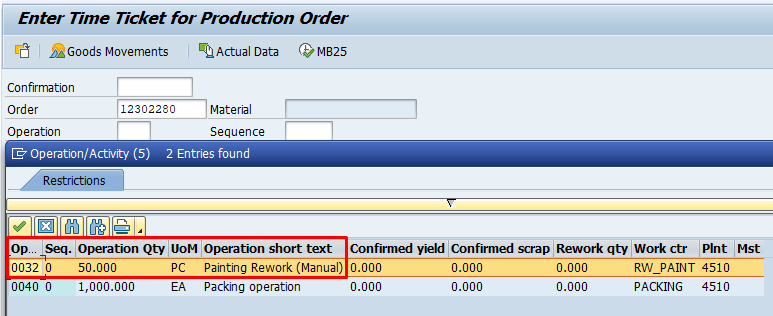
We can see that operation qty. for the rework operation is 50 qty. as there are only 50 qty. rework in OP30.
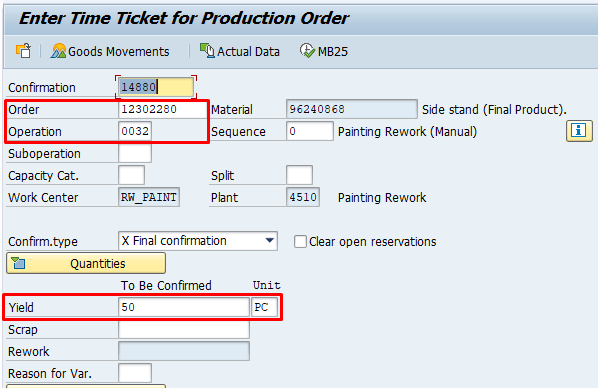
(Note: If you try to skip rework operation & do confirmation of OP40 then yield confirmed qty. will 950 qty. only.)
Save the confirmation OP32.

After this, you can go ahead with the confirmation of last operation & Post the GR against production order. Complete the further process (TECO, Settlement, CLSD).