We are once again in the final quarter of the year, which means that it is time to share with you the latest updates to SAP EWM that came with the SAP S/4HANA 2021 release.
While overall this year was slightly more optimistic than 2020, the world is still feeling the effects from the impact of last year’s events. And while the road to recovery is still ahead, I would like to proudly thank our great development teams for their tireless work and dedication. Thanks to their efforts, we have not slowed down in delivering enhancements that all our customers can appreciate.
In this year’s release we invested in stronger integration, especially in the process flow between production and warehousing. Aside from this, over the year we have constantly worked on enhancing usability and user experience, brought many often-requested features, as well as quality of life enhancements that make our warehousing solution more intuitive and easier to use. In the following article, we will go through the areas of our investments for this release as well as some of the highlights in each area. And we begin with one of our key focus areas of this release, Integration.
INTEGRATION
Plant Maintenance Integration
With this feature, you can manage the material components that you need for plant maintenance with SAP Extended Warehouse Management (EWM). You also have full transparency throughout the maintenance process.
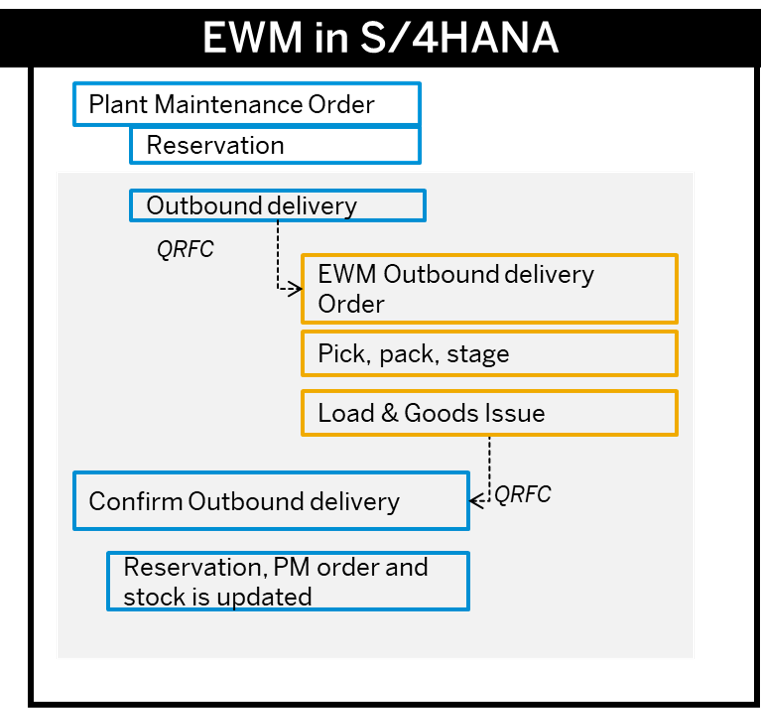
The material components that are requested are staged from an EWM-managed storage location via an outbound delivery order. The outbound delivery order now contains a reference to the maintenance order (PM order) and to the reservation document. The staging area can be determined based on the recipient location that is entered in the PM order. SAP EWM uses different methods to retrieve the recipient location from the PM order, depending on whether you are using EWM embedded in SAP S/4HANA or decentralized EWM based on SAP S/4HANA.
Enhancements to Packing Functions Using Unified Package Building
With this feature, you can create packages using unified package building, a generic packaging layer. Unified package building supports alternative packaging approaches. These packaging approaches are called unified package building engines and process different sets of packaging master data and Customizing settings. The following unified package building engines are supported:
- Package building with the package builder
- Packing instruction
- Packaging specification
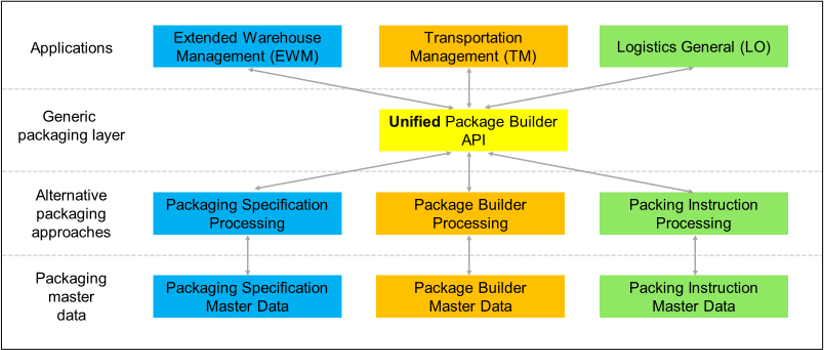
You can use unified package building when a packing proposal is required for the following process steps:
- For receiving handling units (HUs) from production using radio frequency (RF)
- For deconsolidation and repacking inbound deliveries
- For packing in the outbound delivery process
- For packing in the posting change process
- For packing in the stock transfer process
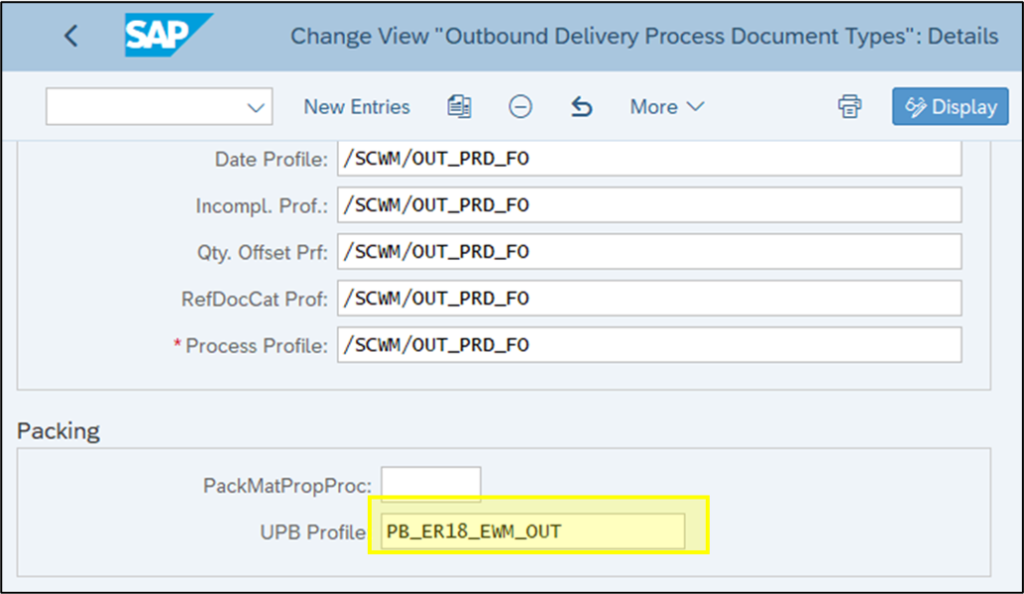
In the linked “What’s New” document (which you can find in the intro or at the end of this presentation) you can see multiple examples of using the UPB for the processes listed above, such as for the process of receiving handling units (HUs) from production using radio frequency (RF).
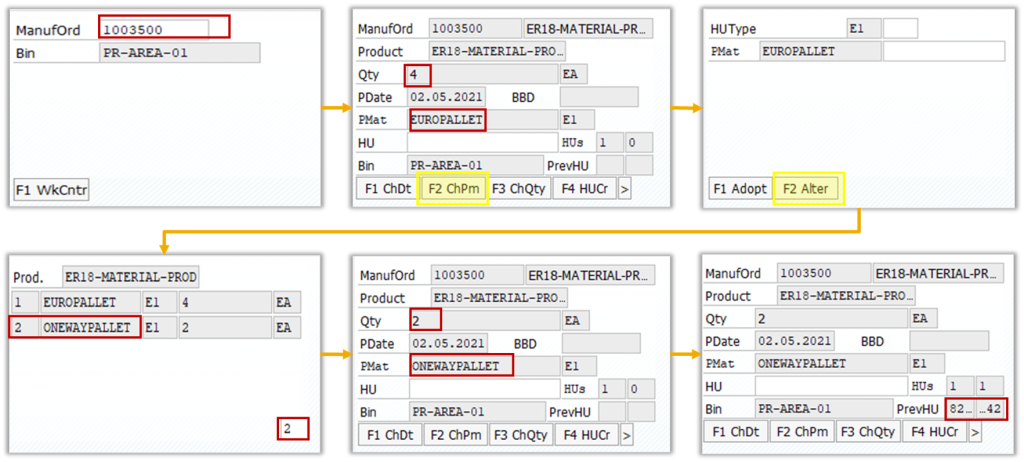
Moving Sample Stock to Quality Inspection
On the Quality Management side, users can now split sample stock from quality inspection stock for a quality inspection. If the stock is packed into handling units (HUs), you can round the sample size to avoid needing to unpack the HU to take the sample.
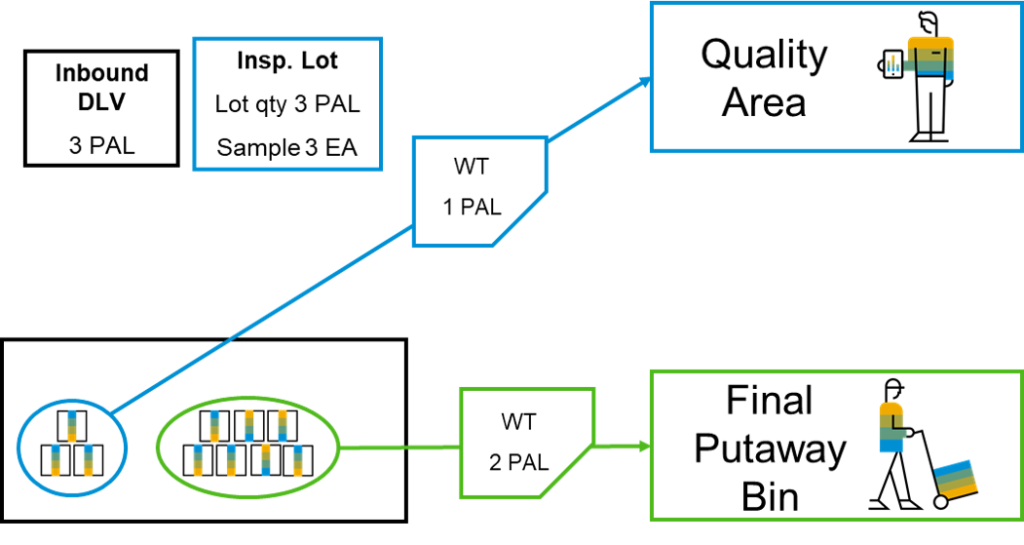
To take sample stock from quality inspection stock, during inbound processing the system uses the sample size calculated in the Quality Management component to create a warehouse task to move the sample stock for a quality inspection. The remaining quality inspection stock in the inspection lot is then put away to the final putaway storage bin.
MES-Driven Staging (SAP DMC)
In this release, one of our primary integration goals was to further strengthen the integration between production and warehousing operations. As a result you can now use MES-driven staging to create detailed plans for fulfilling staging requirements for a manufacturing order, if you’ve integrated your SAP S/4HANA system with a manufacturing execution system (MES). The plans are represented by a document from the MES, the staging request, which is mapped to a warehouse request of the internal stock transfer type in SAP Extended Warehouse Management (EWM).
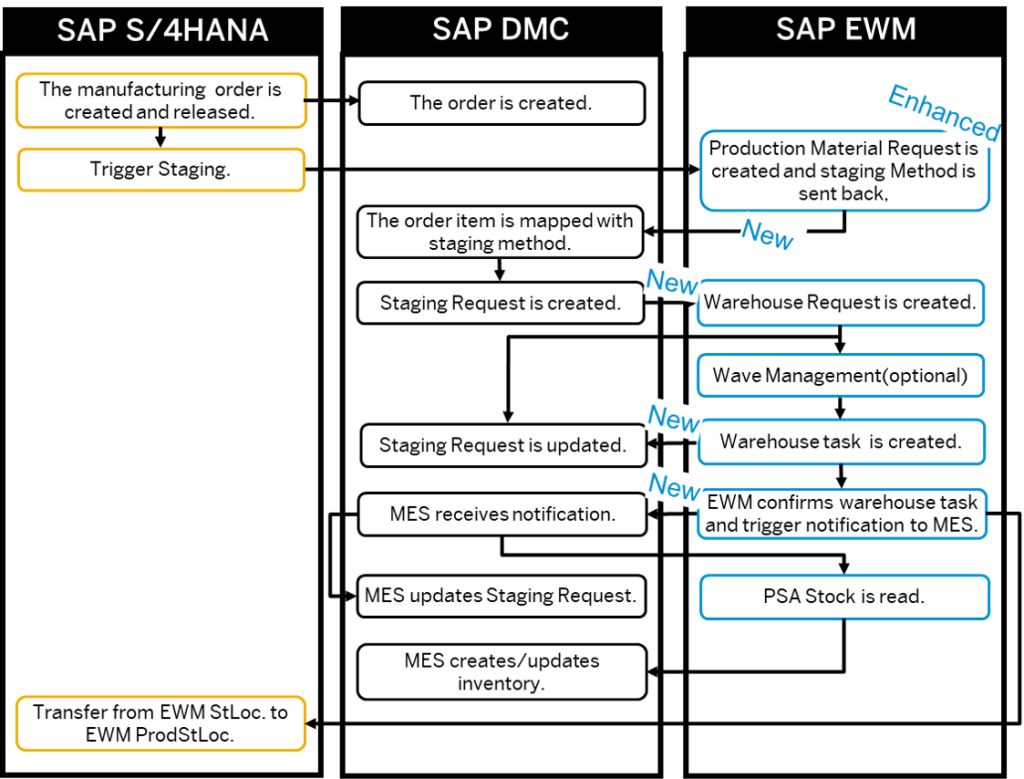
SAP EWM uses a staging report to check the capacity of the bin at the production supply area (PSA) and to create reasonable numbers of staging warehouse tasks. These staging warehouse tasks can be organized, for example, by applying process-oriented storage control (POSC) or waves.
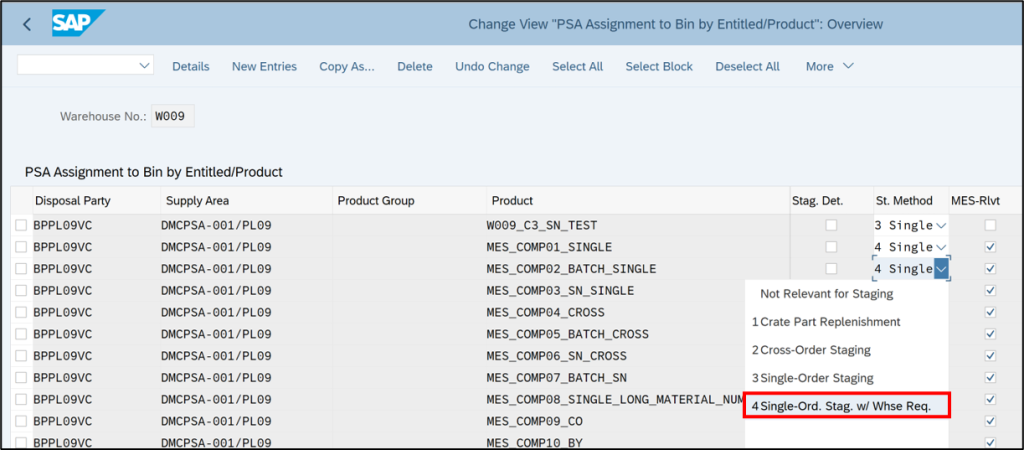
The staging process is transparent from beginning to end. It’s possible to see the status of the staging process in both EWM and the MES. For example, you can see whether a staging request is being planned or has already been executed, or what quantity of a component is requested, in-transit, or staged.
During the MES-driven staging process, you can monitor the status of warehouse processes and communication between EWM and the MES in the warehouse management monitor. In the node Tools SOAP Message, you can monitor incoming and outgoing SOAP messages.
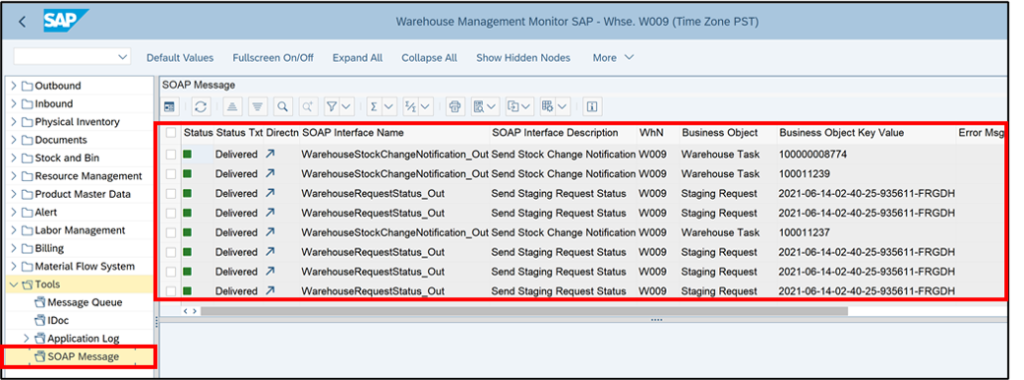
Other Integration Enhancements
Aside from the highlights mentioned above I would like to briefly mention that we also enhanced the new integration between SAP EWM and SAP TM called Advanced Shipping & Receiving (ASR) as well as the integration with MIGO for Synchronous Goods Movement. For ASR we made it possible for users to have the system set the shipping readiness status of a delivery to READY automatically. We also enhanced the “Load or Unload Freight Order” App so that users can view and update the actual quantity in the delivery, view the container unit in the hierarchy of the delivery, see the aggregated gross weight and gross volume, and call up detailed error logs for failed goods movements.
On the Synchronous Goods Movement side, you can post goods movements for unpacked products directly into the warehouse from the “Post Goods Receipt for Purchasing Document” and “Post Goods Receipt for Production Order” Apps. You can also allow the system to determine packing instructions in the Post Goods Movement app based on more criteria than before.
AUTOMOTIVE
Perform Physical Inventory on Production Supply Areas
We continued this year on further enhancements and features to our solution for automotive industry. The ability to perform physical inventory counts on Production Supply Areas is a new feature for SAP EWM. With it, you can perform accurate physical inventory on production supply areas (PSAs), where the amount of stock is constantly changing. When a production worker takes products from a PSA, goods issue posting is often done later as a backflush. To deal with the difference between the stock quantity on the PSA and the quantity in the system, you can link the physical inventory document to a production order using a count reference. The system updates the numbers from the physical inventory count with the goods issue information from the production order. Existing customizing “Reason for Physical Inventory” is enhanced with “Count Reference Flag”. If this reason with this flag is used in the PI document, the count reference should be entered in the PI count & record.
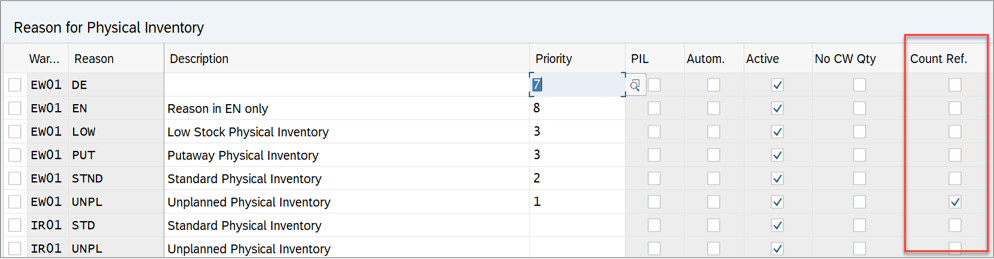
Enhancements to Stock Transfer for JIT Call
We also enhanced the Just-In-Time supply to production process this year with a new scenario, process enhancements and new UI elements. Firstly, regarding the new scenario, you can now stage products to a production supply area that is managed by the Inventory Management (MM-IM) application component for the stock transfer for JIT call process.
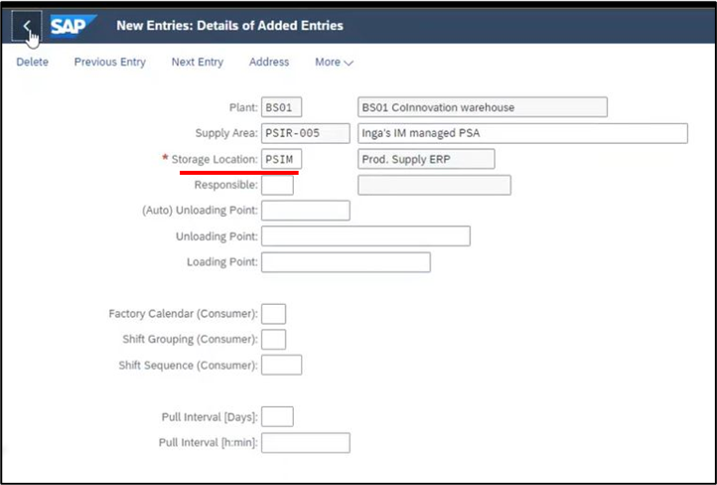
Furthermore, you can redetermine the warehouse process type for stock transfer items, if necessary, and you can block stock transfer items for planning activities. You can also process exceptions that occur using pick denial or bin denial for stock transfer items, and you can cancel or reverse picking warehouse tasks.
If pick denial is triggered during picking preparation for stock transfer items that are assigned to a wave, you can configure your system to remove the stock transfer items from the assigned wave. This allows picking to be replanned for the stock transfer items, which can be assigned to different wave.
If you have to execute a bin denial during picking, you can configure the wave template for the system to remove the item from the wave, without reassigning the item.
As to the UI enhancements we have made the following additions:
- New “Alerts” column in the App “Plan Supply to Production” to display error messages from stock calculation
- New monitor node “JIT Handling Unit ”
- New monitor methods
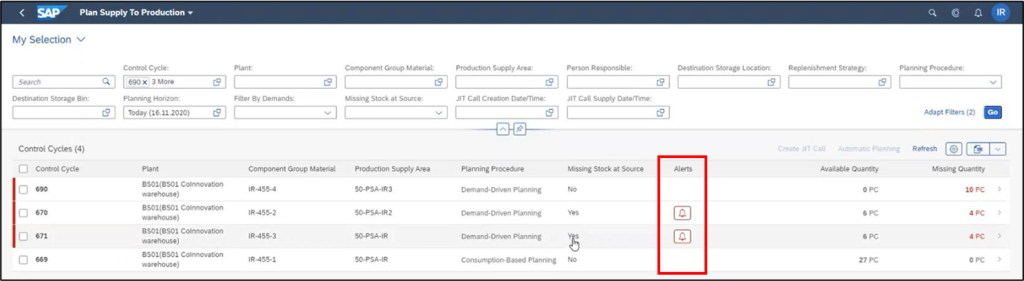
INNOVATIONS
Consolidation of Batches with Date Tolerances
Stock consolidation allows you to form full stock-keeping quantities from partial quantities of stock. With this release, you can consolidate stock of the same material but with different batch numbers within a given date tolerance interval.
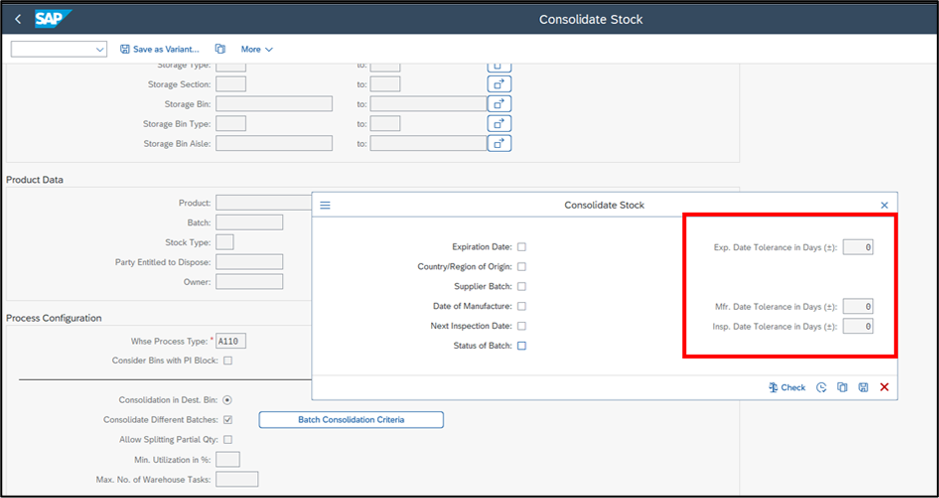
You select the batch criteria that you want to match, and then you get proposals of partial stock to consolidate. In addition to the batch criteria for consolidating different batches, you can also set a date tolerance interval for the following selection criteria:
- Expiration date
- Manufacturing date
- Next date of inspection
The application log for the “Consolidate Stock” App has been enhanced with a tree structure to make it easier to follow the logic of the stock grouping and the generation of the warehouse task proposals.
Attachment for Handling Units
Attachment services is a feature we made available for the On-Premise deployment of SAP EWM since the SAP S/4HANA 2020 release. This year we extended this service to allow users to upload, read, update, or delete attachments in various file formats to handling units (HUs). You can also add hyperlinks as attachments to delivery documents, transportation units (TUs), and HUs.

We support attachments in the Fiori Apps to process deliveries as well as the Fiori App “Monitor Handling Units”. And, as exemplified above, you can also manage attachments directly in the Warehouse Monitor. For that we updated the Monitor to include:
- New method to upload attachments
- New sub-node to list attachments
- Node: Stock and Bin – Handling Unit
- Node: Documents – Handling Units
Please note that if you want to use attachments to handling units that were created in a lower release than SAP S/4HANA 2021, you must migrate the handling units using the migration report /SCWM/R_GEN_MISS_GUID_HU_EXT. Further information can be found in the system documentation for this report.
CDS Views for Storage Bins
CDS Views are de-facto standard for SAP development, and they enable convenient extraction of data for storage space utilization. We have enriched the SAP EWM Virtual Data Model with key figures for Storage. With this feature, you can view some aggregated data relevant to storage bins. For example, the following data is available:
- The number of storage bins that are empty, utilized, or full
- The utilization of storage bins in terms of their weight, volume, or capacity
- The number of storage bins that are blocked, and the reasons for being blocked
Enhance RF Scan Field Length
2D barcodes like DataMatrix or QR-Code are more and more used in a warehouse. Industry standards like VDA (for automotive) or in pharmacy use different data identifiers even with single value barcodes. The solution prior to the SAP S/4HANA 2021 release only supported barcodes with up to 50 characters. Now however you can scan different types of bar codes and longer bar codes (up to 255 characters).
You can enhance the standard bar code logic or define your own bar code decoding logic in Customizing for Extended Warehouse Management under Business Add-Ins for Extended Warehouse Management –> Mobile Data Entry –> Bar Code Specification:
- Initialization of GS1-128 Bar Code Support
- Changing of Application Identifier Types
- Additional Check of Application Identifiers
- Decoding of Bar Codes
- Changing of Application Identifier Data
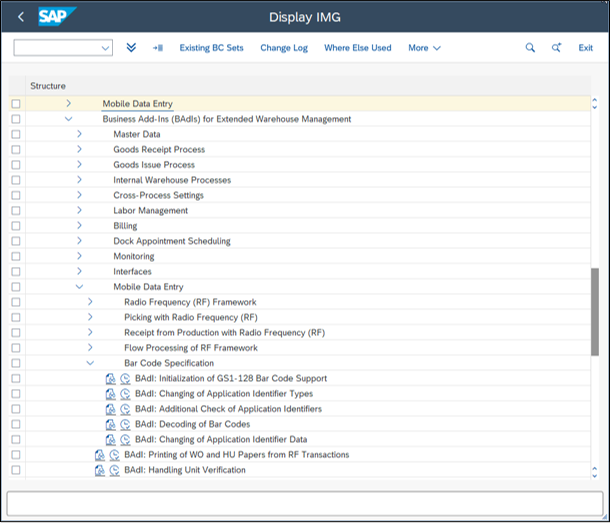
Modernize RF Presentation
There is a new “EWM_MOBGUI” service in the transaction SICF. Via this service, you can display ABAP Dynpro in RF Framework as SAP GUI for HTML. It is optimized for mobile use cases. There are three key advantages for using this service over ITSmobile:
- It requires no generation of an HTML templat
- It renders the RF screens in the most recent SAP Themes and Fiori Design for a modern look and feel
- Screens can be further personalized using SAP Screen Personas
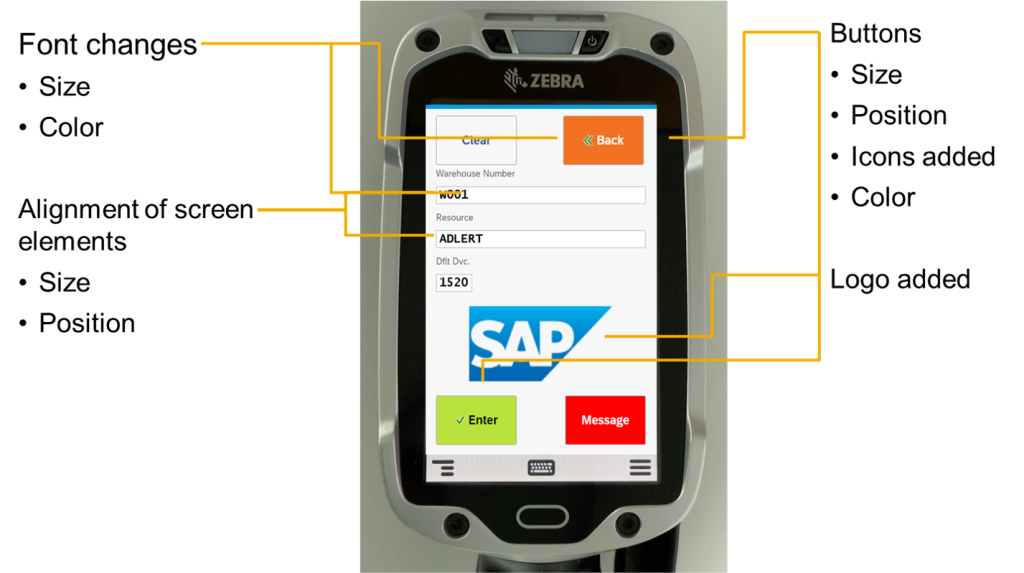
SAP Screen Personas is a brand-new feature, but it is a topic deserving its own article so be sure to keep an eye out for that. We will present in more details what it is, what it does and how you can use it.
USABILITY
New Fiori App “Display Warehouse Documents”
In a typical warehouse, a warehouse document is a goods receipt or goods issue posting which can consist of one or multiple items. You can use the “Display Warehouse Documents” App to select and display warehouse documents which contain all information about a goods movement.
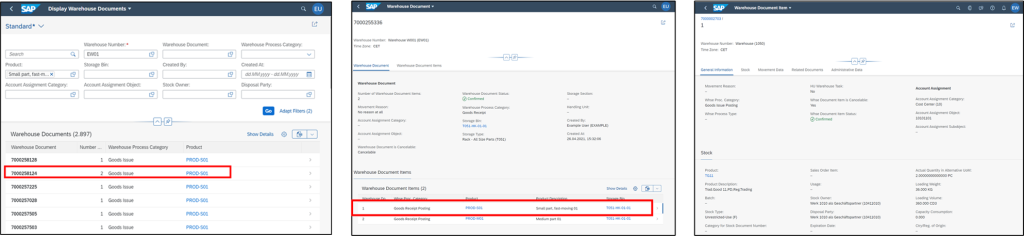
Other Usability Enhancements
Aside from this, we made many other enhancements and fine tunings for the user experience. While they each do not merit and individual subchapter of their own, I would like to quickly mention some of them here:
- In the “Count Physical Inventory” App, you can assign ranges of serial numbers to physical inventory items.
- In the “Pack Handling Units” App, you can resize the split screen and the system then uses this new screen layout the next time you open the app.
- In the “Warehouse KPIs – Operations” App, you can navigate from the outbound delivery order in the drill-down page directly to the “Run Outbound Process – Deliveries” App.
- In the “Run Outbound Process – Deliveries” and “Run Outbound Process – Production” Apps you can change the gross weight and volume of delivery items.
- From the “Run Outbound Process – Deliveries”, “Run Outbound Process – Production”, “Change Inbound Deliveries – Deliveries”, and “Change Inbound Deliveries – Production” Apps you can navigate to the Packing screen. There you can manage handling units (HUs) more extensively, including nested HUs.